- 回首頁
- 機械工業雜誌
摘要:本數據擷取在IoT的技術普及下,產線的狀態可被便利的擷取,而已擷取的數據該如何應用在生產作業中進而解決產線的實務問題是關鍵績效的表現方式。就組裝線而言,為提升組裝效率和產品的品質,虛擬組裝技術可以預先規劃批次產品的組裝工件,同時預測組裝的成品或是半成品的品質。為了提高品質檢測未通過的廢品之再利用,在虛擬組裝中加入廢品企圖最大化廢品的使用率時,衍生計算組裝的時間提高以及成品或半成品的品質不穩定等議題。本文利用二分法降低計算時間,並利用二分法的理論特性推導保證在合理的範圍內計算可最大化廢品使用的組裝指南所需的時間,進而依據問題案例的規模評估所需的計算時間以及成品或半成品的品質。除了縮短虛擬組裝的執行時間,同時也讓組裝產品的品質得以預期。
Abstract:Manufacturers are realizing the importance of process data collection. However, how to interpret process data into valuable business information through analysis is a problem. In this paper, we introduced how to reduce the computational time for the assembly simulation with some scraps. According to the sliding window method, the sequential search can be easily used to find the solution for maximizing the recycling rate of scraps. The major implementation concern is the computation time especially in the large-scale instance. So, we use the binary search to dynamically evaluate the virtual assembly result. The proposed approach successfully reduces the computation time and predict the quality of assembly products.
關鍵詞:物聯網、人工智慧、虛擬組配
Keywords:Internet of things, Artificial intelligence, Virtual assembly
前言
隨著物聯網(Internet of Things, IoT)技術普及,IT人員能夠在產線中輕易的補捉成品或半成品的狀態和製造過程所產生的數據。經過加工、檢測、組裝、品管等作業,資訊系統透過IoT忠實的紀錄所有資訊後,IT分析人員能夠根據目前的狀態預測下一步的潛在議題[1],例如在Ouelhadj與Petrovic的研究中顯示,動態排程根據資源相關的參數和工作相關參數來動態的產生工作排程的規劃[2]。此外,數據分析更能夠協助品管人員回推生產過程中可以改善的作業環節,例如品質關係建模技術(Quality Relative Modeling, QRM)可以動態檢定與推測生產設備的運作是否屬於正常的運作範圍。然而,就組裝線的作業而言,若要提升組裝效率,虛擬組配是一個可行的解決方案[3]。透過產線在檢測作業中所紀錄各個零件的尺寸,計算並列出品質最佳的組裝指南,不旦可以降低重複組裝的重工時間,也可以透過組裝以提升產品的品質。本文針對虛擬組配計算環境中,當待組配工件中含有假廢品時,提出一個能夠提升虛擬組配的計算效能方法,在大量組配需求下迅速的計算出虛擬組配方案。
檢測數據紀錄
為了掌握各個產品的生產履歷,紀錄工件在每個階段的加工資訊是必要的條件,除了高階的二次元與三次元量測之外,在不需要相當精密的量測工具已經相當成熟,例如具無線傳輸的游標卡尺可以讓檢測人員迅速的記錄每個工件指定部位的尺寸,後台程式能夠在收到數據後依據腳本存入指定的工件屬性中,檢測流程如圖1所示。如此一來,檢測人員能夠迅速的將所有工件的各項數值偵測後拋向後台的儲存平台。過去的量測會因為檢測人員的特質而造成量測的品質或是效率有些問題,而在半自動的檢測流程中,ICT系統已協助完成最耗費時間的記錄作業,讓整體的檢測作業執行速度大量提升。
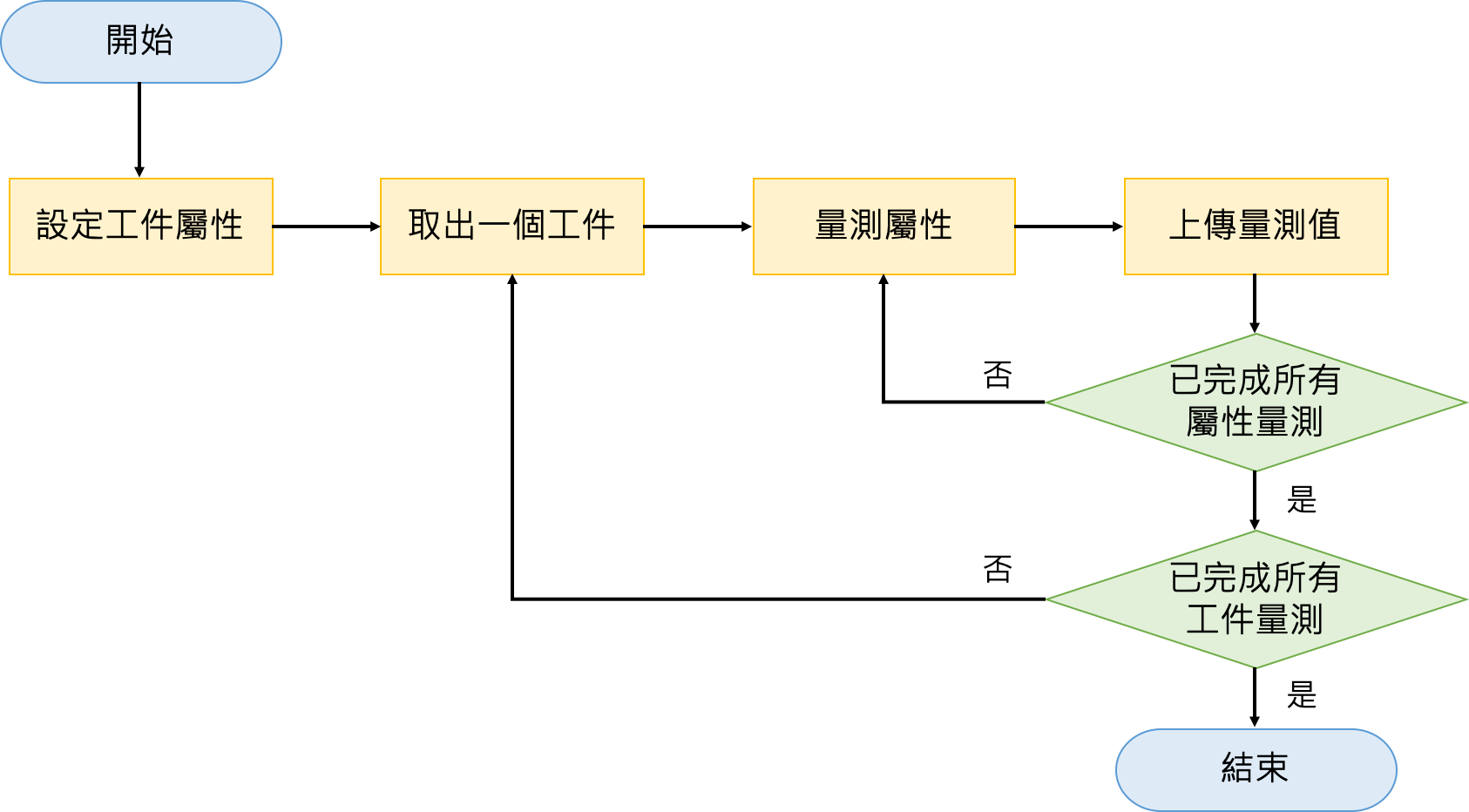
工件組裝
組裝線上的組裝員在收到待組裝的批次工件後通常會隨機的取出各部位的工件組裝,傳統的組裝作業員會依據組裝步驟完成一個成品或半成品的組裝作業。然而,由於各個工件在不同時間加工所得到的尺寸不盡相同,因此,組裝員可能遭遇因尺寸不合而無法組裝的情況。此時的組裝員有兩種執行策略:放棄無法組裝的工件,由其它工件中隨機取出一個工件再組裝;或是利用工具擴孔或是修邊,手動修正工件尺寸以符合能夠接受組裝的狀態。
傳統的組裝存在著組裝效率不佳和產品品質不穩定的問題。一但組裝作業員嘗試組裝無法組裝的工件時,因為反復嘗試不同工件的組裝或是二次加工都造成了組裝時間的增加。另一方面,若組裝作業員採取二次加工,那麼完成組裝的成品或半成品會因為人工的修正而造成品質不穩定也無法預期的現象。
虛擬組配解決方案
透過IoT和半自動檢測技術,檢測員可以有效率地紀錄每個工件的各個屬性的尺寸,而這些尺寸可以提供給虛擬組配作業,以批次計算組裝指南。給定一個待組配的批次工件,每個工件皆被標上工件編號,透過工件編號可以取得該工件的所有量測尺寸,如此一來便可以掌握所有工件的各項屬性的尺寸。透過最佳化演算過程,虛擬組配最終產出一組組配的指南,明確的指出組裝每一個成品或是半成品所需的工件編號,以及預估各個成品或半成品的各項尺寸,以確保產品的品質。
回文章內容列表更完整的內容歡迎訂購 2019年08月號 (單篇費用:參考材化所定價)