- 回首頁
- 機械工業雜誌
[ 最優良文章 ] 應用3D列印陶殼模鑄模技術控制鑄造製程金屬凝固行為及其縮孔
作者 洪珮純、郭信宏、蔡和霖
刊登日期:2019/12/01
摘要
利用積層製造技術於陶殼模鑄模設計,可依照鑄件品質需求,製作出厚薄不均一陶殼模鑄模,達到控制冷卻速率及凝固時產生縮孔形成位置。藉由鑄造製程模擬模組建立及預測分析結果顯示,隨著澆冒口部分之陶殼模鑄模厚度增加,縮孔位置會朝向澆冒口端移動,降低缺陷於鑄件內部形成,對於鑄造製程提供有效改善品質的方法。
For the casting industries, the ceramics shell mold with uneven thickness is fabricated by additive manufacturing techniques. It benefits to control the cooling rate and shrinkage porosity formation during casting process depending on the numerical modeling. The casting quality is improved by the increasing the riser thickness of ceramic mold since the shrinkage porosities were formed toward the riser zone.
關鍵詞(Keywords)
噴膠製程、陶殼模鑄模、鑄造製程
Binder jetting, Ceramic shell mold, Casting process
前言
全球鑄造產業於2018年產值約為221億美元 [[i]],根據全球商業風險與產業分析報告(Global Info Research Business Risk & Industry Analysis Reports)調查,預估精密鑄造產值由2017年198億美元至2023年245億美元,其年複合成長率約為3.6% [[ii]]。鑄造業是國內重要基礎工業,廣泛應用於金屬製品、機械零件等製造業。其中精密鑄造具有表面細緻度高、尺寸精度佳與適用於多種合金鑄造優勢,普遍應用於航太、能源、生醫等高階產業用之小型零件開發為主。
近年來,隨著精密鑄件產品趨向複雜化(厚薄不均)、一體化及大型化應用,對於鑄件尺寸精度與表面細緻度提升需求日趨嚴苛。然而,傳統精密鑄造陶殼模鑄模製程包含開立射蠟模、反覆沾漿淋砂、乾燥、脫蠟、燒結等繁雜工序,以及無法控制模壁厚度;若產品開發屬於大型或厚薄不均之特性時,容易因為凝固行為控制不佳,造成鑄件厚薄區凝固速率不同,於凝固速率小之區域因為凝固行為造成體積收縮,且無多餘金屬液補充,即可觀察到該區域有鑄造縮孔現象發生[[iii]]。為了避免縮孔缺陷形成影響鑄件品質,傳統陶殼模製程過程中,針對鑄件特徵較厚區域,特別增加更厚澆冒口設計,藉此各區塊保溫、散熱、冷卻之速率控制,進而達到控制整體金屬液於模穴之凝固方向性;但此方法常造成材料利用率下降並增加鑄件的後處理工序,導致製造成本增加。
根據多篇研究結果顯示利用積層製造技術製備陶殼模鑄模,可以提供鑄模彈性化設計及提升精密鑄造鑄件品質[[iv]-[v][vi]],對於少量多樣之創新產品開發,更可以縮短產品開發時間50%以上與降低研發成本75%以上。其中噴膠黏粉技術(Binder jetting)可適用於多種類粉末材料與黏結劑,噴印過程於常溫常壓下即可進行,噴墨頭接收驅動訊號後直接將黏結劑噴印圖案於粉床(Powder bed)上,將粉末黏結成形,隨後以逐層堆疊方式建構出初始物件 (Green part),製作大型化物件,而未噴印粉末可回收再回到噴印製程中,此陶殼模鑄模製作方法已成為主要發展製程技術重點之一。
本文主要聚焦於陶瓷粉體積層製造方法應用於一體形精密鑄造用陶殼模鑄模之關鍵殼模設計參數,並整合3D列印無形狀限制優勢進行鑄造模擬及方案設計技術,探討不均厚陶殼模鑄模設計對於控制鑄件各區塊之凝固速度,藉此達到預測分析精密鑄造過程中金屬液凝固行為/方向及縮孔缺陷形成之關鍵影響因素,提供發展3D列印陶殼模鑄模之研究開發基礎。
精密鑄造製程技術
精密鑄造法,又稱脫蠟法(Lost wax casting),具有可鑄造出更薄、形狀更複雜、表面光度佳、尺寸精密度高及生產速度快之優勢。其製作過程包含射製蠟模、組立蠟樹、反覆沾漿、淋砂、脫蠟與殼模燒結、熔解與澆鑄如圖1所示,其中沾漿淋砂在於控制鑄造用殼模模具之壁厚,進而影響陶殼模鑄模的強度與金屬液凝固速度,近年來,相關報告研究殼模厚度、殼模熱傳係數對精密鑄造凝固速度的影響,隨著殼模厚度增加,有效降低殼模中之金屬液凝固速度,且透過不同熱傳導係數(20 ~ 80 w/mk)之陶殼模材料應用,金屬液凝固時間減少44%以上,由此可知,若能夠有效控制殼模的厚度與熱傳速度,將有效控制金屬液凝固速度,並且能夠影響鑄造產品的微觀組織,調整鑄件品質及性能。
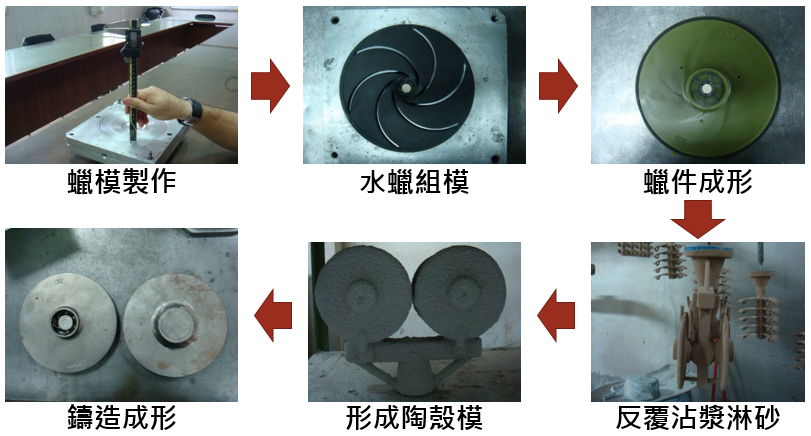
圖 1 精密鑄造流程圖
精密鑄造凝固原理與鑄件品質改善方法
熔融金屬澆注至陶殼模鑄模中便開始冷卻,由澆注液態金屬完全凝固所需時間稱為凝固時間,鑄件內部在凝固過程中因金屬液本身熱脹冷縮的特性,在冷卻凝固的過程中,高溫金屬液補充其凝固收縮,而產生體積收縮的現象,收縮過程分成為三階段(1)熔融金屬液澆注後,液態金屬降溫過程會產生0.5%的液態收縮(Liquid contraction);(2)由接觸陶殼模鑄模模穴的金屬液開始形成凝固金屬表層,即鑄件表面,而金屬液態凝固成固態過程中,由鑄件表面往內部凝固會產生凝固收縮(Solidification shrinkage)、(3)固態元件於降溫過程中低溫區產生拉應力,造成固態熱收縮(Solid thermal contraction),故從最後步驟了解到,鑄件內部凝固的速度較遲,容易造成鑄件內部或表面產生凹陷或不規則的孔洞,稱為縮孔(Shrinkage porosity)如圖 2所示。
傳統鑄造製程,皆以設計補充流道(Feed channel)、進模口(Gate)、冒口(Riser)等來獲得方向性凝固使鑄件得到足夠金屬液補充如圖 3。改善鑄件品質常藉由鑄造方案設計,克服模壁逐漸向中心凝固的現象稱之漸進式凝固(Progressive solidification)狀況,使鑄件每一個部分於凝固過程中都能夠由補充澆道獲得金屬液補充,即所謂方向性凝固(Directional Solidification),主要是利用溫度梯度控制穩定且定向的熱傳方向,使液態金屬在凝固的時候是以單方向往熱傳的反方向進行,延長冷卻凝固時間,降低並改善較厚斷面內部缺陷。
然而,凝固過程中固液界面受到溫度梯度、凝固速度及溶質濃度等影響,可分成四種型態如圖 4所示。固液介面的初始凝固行為導致微小預凝固點生成,若固液界面的液相區溫度高於熔點,此凝固點則再次熔合,呈現Planar的固液介面;當固液介面溫度略低於熔點,預凝固點將持續成長,稱之Cellular現象;當主要固液界面溫度梯度漸緩,會使Cellular成長至Dendrite狀態;甚至溫度梯度達一定臨界點時,液相區不受主要固液介面影響,Free Dendrite於液相區獨立生成。固液介面以Planar形態為佳,輔助方向性凝固減少縮孔的效果,據文獻指出溫度梯度大、凝固速度小、初始濃度小時,則有利於方向性凝固的效果。根據上述原理說明,若能夠利用不同殼模厚度設計,來建立殼模本身的溫度梯度變化,達到控制殼模熱傳,進而影響金屬液凝固速度與方向的傳遞控制,將有效建立出良好的方向性凝固趨勢,促使鑄件缺陷降低與良率改善。
回文章內容列表更完整的內容歡迎訂購 2019年12月號 (單篇費用:參考材化所定價)
主推方案
無限下載/年 5000元
NT$5,000元
訂閱送出