- 回首頁
- 機械工業雜誌
- 歷史雜誌
摘要:在高效率航太加工與高精度需求的模具加工中,過切一直是關鍵的問題點,造成過切的因素可分為CAM工法規劃與機械振動兩大類,針對過切問題,使用者常在機台調機與加工刀法規劃上尋求解決,但業界目前仍無明確的科學化模型。
本文整合CAM路徑規劃模組與工具機機電系統,首先對CAM的品質進行確認,包含極短反向背隙與減速率及減速數量…等指標,接續整合機電分析模組進行刀尖點誤差分析,並將其三軸向動態誤差轉換為模面法向誤差,最終在模面上以色點後處理方式呈現誤差分佈,使用者即可以快速進行切削模擬預測加工狀況,並透過調整CAM工法規劃或重新設計機台動態響應…等方式進行加工模面的誤差狀況修正,有效連結CAM路徑規劃與機台動態響應之間的關係,建立相對應的科學化模型。
Abstract:Under-cutting has always been a key issue in high-efficiency aerospace machining and high-precision mold processing. The overcutting factors can be divided into two broad categories: CAM machining strategy and mechanical vibrations. Users usually deal with the overcutting problems by tuning machine or taking alternative machining strategy. But there is still no clear scientific model can be referenced.
This paper integrates the CAM path planning and the mechatronic system of machine tool. Firstly, the quality of the CAM model is confirmed, including the indicators of extremely short reverse backlash and deceleration rate and quantity. Then, the mechatronic analysis module is integrated to analyze the tool center point error. The three-axis dynamic error is converted into the normal error of the die surface, and finally the error distribution is presented on the die surface by the post-processing method. The user can quickly perform the cutting simulation to predict the processing condition and adjust the CAM method, or re-design the dynamic response of the machine to correct the error condition of the machining die surface. The proposed method effectively links the relationship between the CAM path planning and the dynamic response of the machine to establish the corresponding scientific model.
關鍵詞:過切、機電整合、切削模擬
Keywords:Under-cutting, Mechatronics, Cutting simulation
前言
台灣為全球工具機出口大國,產業分布型態以中小型企業居多,近年來在面臨國際大廠客製化設備技術優勢競爭下,國產工具機勢必需在設計端與應用端進行結構性的創新來縮短技術差距;在設計端來說,國內工具機產業雖已漸漸導入CAE電腦模擬分析技術於機台開發,但大部分仍以靜態剛性分析與模態分析為主,分析結果尚未足以直接與加工使用者所在意的切削效率與切削精度連結,導致經常發生機台開發完成後加工效率不符合客戶預期或模具表面加工紋路異常現象;在應用端來說,針對加工表面紋路異常問題,常在機台調機與加工刀法規劃上尋求解決,但現場仍以試誤法為主進行測試,無法建立相對應的科學模型。
本文整合CAM路徑規劃模組與工具機機電系統,導入於設計端可針對客戶的產品CAM路徑進行機台效能預測,並客製化產線機台;導入於加工應用端可根據機台響應特性進行最適化CAM路徑規劃,透過連結工具機機電系統與CAM之間的關系,針對加工表面紋路異常問題,建立相對應的科學模型,協助設計人員與加工人員在機台的開發與應用上能提高操作效率。
CAM路徑規劃分析技術
不管在高效率航太加工或高精度需求的模具加工,過切一直是關鍵的問題點,造成過切的因素可分為兩大類:
1.CAM規劃的品質好壞:包含工法、單節長度、單節夾角…等因素,
2.機械的動態誤差與振動:加速度導致的刀尖點誤差與振動量。
針對過切此問題,業界一般會以經驗法則調整CAM的路徑規劃進行測試,或以調機方式降低加速度解決,但總體來說對於解決方法尚無明確的科學化模型,本節將針對CAM規劃之路徑工法進行探討,並提供一CAM品質檢查指標與工具。
1.極短背隙反向點檢查
周[1]提出CAM計算路徑座標時,不管解析度多高,控制器讀入後會在最小單位的下一位數做四捨五入的處理,例如在最小單位1 μm的控制器系統中,0.499 μm以下會被視為0 μm,而0.5 μm以上則被視為1 μm,CAM路徑規劃中的0.001 μm誤差在控制器中會變成1 μm,這即是因解析度造成的問題;舉例來說,當在進行一個平滑曲面加工時,Z軸向有可能因解析度的問題產生1 μm的反向移動,如圖1,若機械結構的背隙或磨擦問題較大,或是控制器尖角補償的不夠合適時,在該反向點就有可能發生振紋。
本文建立一專家模組進行反向背隙檢查功能,如圖2,背隙分析的目標在判斷軸反向發生次數以及位置,這些區域在尖角補償沒設定好時會產生異常切削痕跡,其流程如下
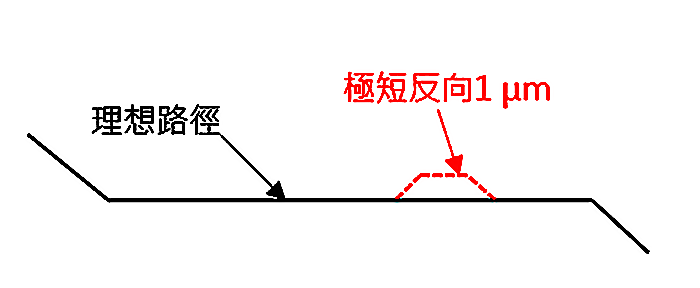
圖1 因解析度問題產生的極短反向示意圖
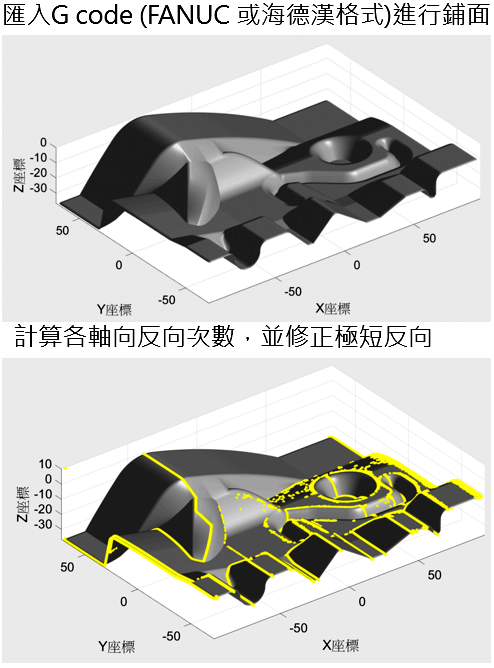
圖2 反向背隙檢查模組示意
回文章內容列表更完整的內容歡迎訂購 2018年11月號 (單篇費用:參考材化所定價)
主推方案
無限下載/年 5000元
NT$5,000元
訂閱送出