- 回首頁
- 機械工業雜誌
- 歷史雜誌
摘要
本研究在傳統拋光製程後利用微能量束作形狀修整技術,以達到高精度品質之玻璃透鏡。大氣電漿噴嘴設計為以RF射頻電源驅動噴流,並藉由內外雙套管的設計,於內管內導入電漿製程氣體,外管導入限制電漿束尺寸的惰性氣體,以此調控內外氣體種類以及流量,實現單一噴嘴以氣流侷限方式控制電漿中央區的範圍以調控能量束口徑狀態。 本實驗同時採用光學放射光譜儀分析電漿物種隨氣體比例以及功率等參數的變化,了解電漿反應與表面狀態、蝕刻速率的關係,以獲得一最佳的拋光參數。 由實驗結果得知玻璃透鏡表面之蝕刻率可控制在50 nm/min至450 nm/min,表面粗糙度可達< 5 nm。
Abstract
In this article, method of finishing lens' shape using micro-energy beam after polishing process is proposed to achieve high quality lens. The project aims to design a dielectric barrier discharge (DBD)-based micro-energy jet, of which jet is an atmospheric plasma jet configured from a double tube with fine focused plasma for local polishing. In this study, the etching performance and main characteristics of this jet tool are discussed in the context that the plasma light intensity from highly reactive fluorine atoms and other radicals can be well defined using optical emission spectrometry. The results reveal that the etching rate can achieve 50 nm/min to 450 nm/min and surface roughness (Ra) remain lower than 5 nm after plasma treatment.
關鍵詞:大氣電漿、光學玻璃透鏡、拋光
Keywords:Atmospheric plasma, Optical glass lens, Polishing
高精度大口徑之矽基玻璃光學透鏡為先進光學系統之關鍵元件,高階鏡組採非球面或非對稱設計,而傳統面接觸式彈性拋光在製程良率上遭遇瓶頸。 傳統以接觸式的化學機械研磨、磁流拋光及離子束拋光來修整鏡面表面缺陷,然而其工作原理分別為化學機械式材料移除、磁性粒子機械式移除及高能量離子束將透鏡表面原子進行轟擊修整 [1-2]。 離子束拋光因移除量為原子等級,故加工時間較長,且在真空加工環境下限制及建置設備成本高,因此目前仍停留在學術單位及研究機構中;在磁流拋光技術上,具有比離子束拋光更高的生產效率,然在設備的建置成本仍是高於傳統數十倍,無法適用在量產線上,且所需的抛光液為微米級的高磁導性粒子,容易因氧化而產生銹蝕,造成抛光液不能回收。 故利用大氣電漿作拋光除了可在大氣環境下實現,其具有量產性及設備成本低等特色[3-7],在球面與非球面透鏡加工方式上採用局部拋光修整以提高精度,但每當透鏡重工後會產生新的形狀變異性,藉此掌握精度控制與縮短完工時程。 國外鏡片加工知名研究單位(Leibniz Institute, Cranfield U.)發展出非接觸式常壓電漿拋光技術[8],可在微區進行形狀修整,惟目前屬高溫製程(≥300℃) ,造成鏡片變形與表面品質不佳。
本研究主要目的為藉由非接觸式能量束處理,以有效達成拋光的目的,減少材料表面機械式拋光所造成的損傷層。 在大氣電漿噴嘴之設計為以RF射頻電源作驅動噴流,並藉由內外雙套管的設計,於內管內導入電漿製程氣體,外管導入限制電漿束尺寸的惰性氣體,藉由內外氣體種類以及流量的調控,實現單一噴嘴以氣流侷限方式控制電漿中央區的範圍,調整電漿束使可進行毫米等級大範圍粗拋以及奈米等級的精拋,並透過流場模擬將噴頭結構最佳化。 在實驗過程中,可調控大氣電漿Ar離子強度與高反應性分子比例與流場,控制反應性化學根的空間濃度分布呈現高斯分佈,運用表面形貌量測儀器,以精確掌握微小區域的材料去除率。 同時採用光學放射光譜儀分析電漿物種隨氣體比例以及功率等參數的變化,以此了解大氣電漿反應與光學件表面狀態及蝕刻速率的關係。
電漿拋光製程技術
在開發微小雙套管RF低溫電漿噴頭(孔徑≦ 150μm)上,本研究透過外管氣流量以及氣體種類調控電漿束口徑尺寸,使電漿噴流呈現高斯分佈,避免加工前後之熱脹冷縮,以維持精密拋光加工之精度。 在大氣反應性離子蝕刻電漿製程中,除採用CxFy化學蝕刻效應,添加可提升F/C ratio轉化物質,同時利用Ar離子作物理轟擊並提升電漿準直性及反應速率,使透鏡表面轉化形成SiF4, SiF2, CO, CO2, COF2等氣態物種,達成非接觸式材料移除的目的。
1.雙套管電漿系統架構及電漿拋光測試平台
本研究大氣電漿拋光機台為使用RF 13.56 MHz電源供應器,雙套管電漿結構設計如圖1(a)所示 [9]。 內管的流道為主要電漿產生氣體的通道,用以通入維持電漿產生的Ar以及反應氣體如CF4、O2; 電極設置於內管外側,藉由氣體流經電極間電場將氣體解離後而形成電漿狀態。 內管採用介電材質石英玻璃,其出口為直徑2 mm;外管與內管間的流道則作為惰性緩衝氣體的流道,其作用為減少外界氣體參與反應影響電漿氣體組成並增加電漿的穩定性以及作為電漿束縮束用。 機台整體的架構如圖1(b)所示,將雙套管電漿源放置於一X-Y-Z移載平台上,可使用移載平台控制器調整電漿源與待處理物的相對位置。 在移載平台下方設有一拋光平台底座,具有一個可旋轉的基座,由皮帶輪銜接至馬達帶動,藉轉速控制器調整轉速大小,其旋轉基座下方設有一接地導桿,作為接地電極使用,並設有可銜接恆溫循環水槽的銜接口,可控制溫度於10℃-90℃。 能量束模組電極接點由電極設置處延伸至上端基座已利電性銜接。 電極除作為電性銜接用,亦作為固定內管的位置,使其對準氣體出口用。 圖1(c)為大氣電漿拋光實驗過程狀態,在利用部分離子化氣體生成主要靠電漿內部物種的碰撞反應,靠電子在電場中加速獲得極高動能,而當它碰撞到氣體物種時進行能量傳遞應進而達到離子化。 電子動能與電場間可由電場對電子作功累積表示之,亦即電子所獲得的能量相當於粒子帶電量、電場大小及其粒子平均自由路徑之相乘。 電漿蝕刻具有高能量離子及具有反應性之自由基,在它與基材表面接觸時,離子的撞擊與反應自由基的作用,將會與基材形成揮發物而帶離基材表面來達到蝕刻目的,故本研究以含氟自由基蝕刻矽基玻璃光學透鏡之反應式如下所示:
SiO2(s)+CF4(g)→SiF4(g)+SiF2(g)+CO(g)+CO2(g)+COF2(g)+SiOF2(g)+O2(g) (1)
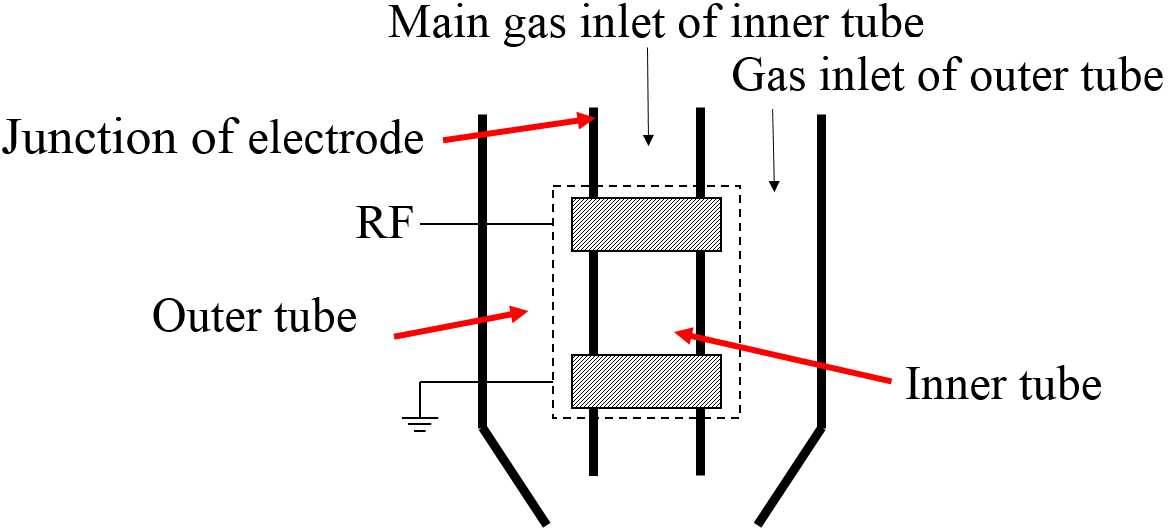
(a)
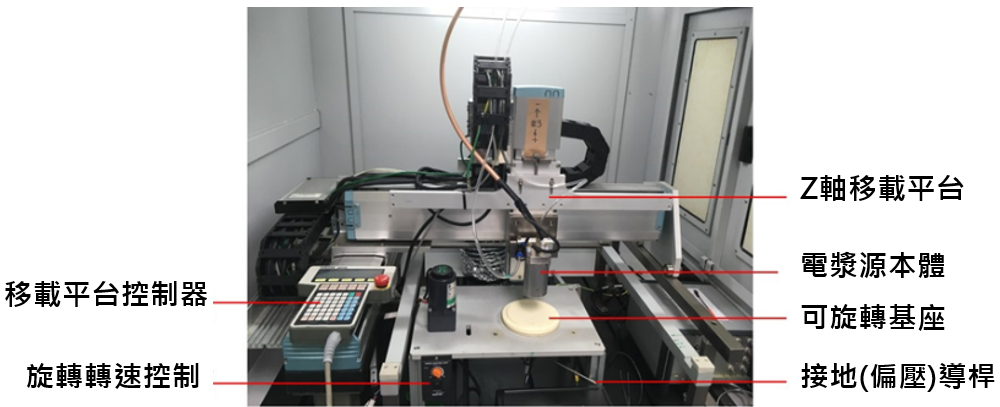
(b)
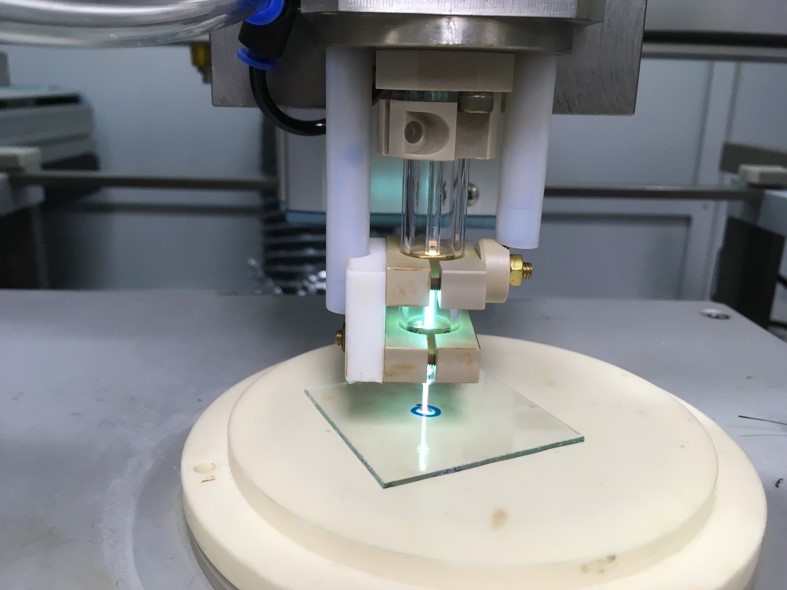
(c)
圖1 (a)雙套管能量束系統示意圖[9], (b)電漿拋光測試平台整體圖及 (c)電漿拋光製程技術
2.電漿物種電漿光譜分析
在電漿拋光模組上架設一電漿放射光譜儀(Optical Emission Spectrometer, OES)系統,以量測電漿激發放出的光譜作為參數調整依據。 電漿放射光譜儀系統由聚焦鏡、光纖、分光儀以及光電倍增管組成,架設方式為將聚焦鏡以及光纖組設置於電漿噴嘴前方,移動XY平台調整聚焦鏡以及光纖組與電漿噴嘴的相對位置,使聚焦焦點位於電漿束預測量的位置,在收光後經光纖傳輸至分光儀,經分光後傳至光電倍增管擷取訊號作後續分析。
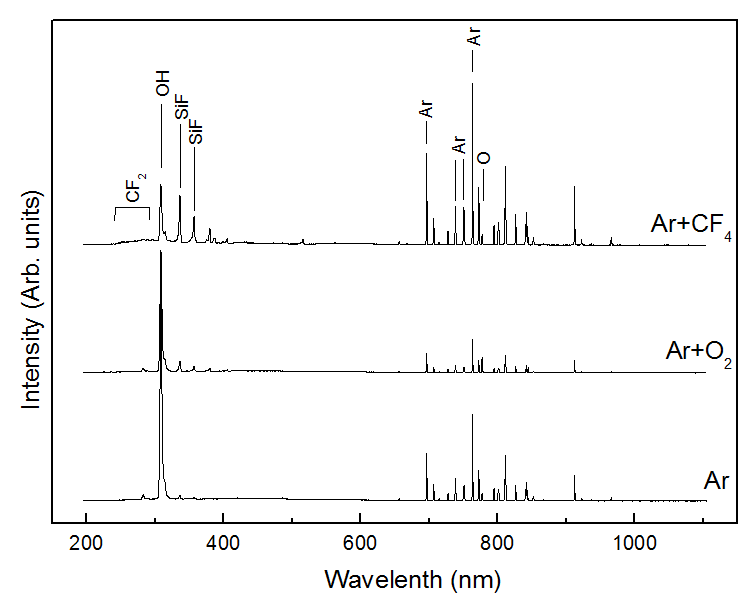
圖2為電漿電漿功率固定於70 Watts,分別量測Ar (4 slm)、Ar+O2 (30 sccm)、Ar+CF4 (9 sccm)三種電漿激發光譜。 在純Ar電漿中,所量測到的光譜在波長600-800 nm間可發現屬於單原子Ar的線激發光譜,在波長306 nm的位置,可找到OH的特徵光譜,此特徵光譜為Ar電漿激發後與周遭氣氛的氧氣或水氣反應形成;在Ar+O2的光譜中,光譜與Ar電漿的特徵峰值相同,但於777 nm屬於O2的特徵峰值增加;在Ar+CF4的電漿光譜中,則除了Ar、OH的峰值顯著外,在336 nm、356 m以及200-300 nm間可觀察到SiF以及CF2的特徵峰值,顯示CF4被電漿解離;而存在SiF特徵峰,係因裝置的介電層以石英材質製成,CF4激發後與管壁作用而產生SiF特徵峰。
回文章內容列表更完整的內容歡迎訂購 2019年09月號 (單篇費用:參考材化所定價)
主推方案
無限下載/年 5000元
NT$5,000元
訂閱送出