- 回首頁
- 機械工業雜誌
- 歷史雜誌
砂模鑄造之自動生成最佳冒口的系統
作者 洪啟銘、馮玉麟、許富淵
刊登日期:2021/12/01
摘要
在金屬鑄造製程中,鑄件成型時的凝固熱點通常會形成縮孔缺陷,因此在進行鑄造方案設計時,需判斷凝固熱點位置,並在此位置設計冒口(feeder),以消除縮孔的發生。一般而言,運用鑄造成型模擬軟體,可判讀出鑄件成型的縮孔位置,但模擬軟體價格昂貴,且模擬完成的時間常在數小時以上。本文“自動生成最佳冒口的系統”可幫助鑄造界真正解決複雜鑄件形狀的冒口設計,是屬於專門的電腦輔助應用於鑄造冒口方案設計(Computer-Aid for Feeder Design)的重要軟體。可以讓設計者在第一時間,由軟體計算便可以得到正確的最佳化冒口設計,不需要再使用試誤法。因此,本文所構想的新一代系統,可以提升鑄造界轉型、讓鑄造界可以縮短開發時間,以及節省不必要的成本浪費。
Abstract
In the metal casting process, the solidification hot spots developed during casting molding usually form shrinkage defects. Therefore, when designing the casting runner system, it is necessary to determine the location of the hot spots during casting solidification and design a feeder at this position to eliminate the occurrence of shrinkage. Generally speaking, the casting molding simulation software can be used to determine the position of the shrinkage cavities of the casting, but the simulation software is expensive. Furthermore, the simulation takes a very long time. This paper introduces computer-aided software to optimize the feeder design for castings with complex geometry. It helps designers to get the correct and optimized feeder design through short-time simulation based on the algorithm embedded in developed software, without going through the trial and error process.
前言
鑄造之凝固模擬在鑄造界已經有廣泛的應用,許多商業用凝固模擬軟體已經達到相當地準確度,與實際鑄件缺陷也得相當的驗證。但是,真正要能解決複雜形狀的鑄件問題時,則需要有下列前提:
1. 冒口方案需要有經驗的工程師設計。
2. 工程師需許多次的試誤法測試最佳冒口設計。
3. 工程師需要有電腦模擬以及實際鑄造的知識。
因此,許多複雜形狀的鑄件往往需要經歷過多次的試誤法得到經驗,但是這些經驗無法在每次的新開發鑄件得到真正精確的冒口大小及數量的設計。
為了縮短這個開發時間,因此許多學者開始 [1-2] 應用所謂鑄造知識為基礎的專家系統 (knowledge-based expert system) 資料庫,來輔助冒口方案設計。從所建立的冒口資料庫系統,分析建議可能的冒口方案設計(沒有建議正確的冒口數量和尺寸)。但是,這個系統只是提出經驗和參考資料,無法真正解決實際鑄造問題。
如果要解決實際鑄件的凝固問題,必須先了解凝固過程中,凝固缺陷形成的方式。所以凝固過程時,固-液界面的形成方式,以及其移動過程與凝固速率和凝固時間之間的關係,變得極為重要[3-4]。而固-液界面的形成,是因為模穴中的金屬液體與模壁接觸時,冷卻過程中有三個形式的熱傳遞:
1. 熱經由凝固的金屬傳出模子外以熱傳導方式。
2. 熱在模子外部以對流方式傳出於空氣中。
3. 以及熱在開放式的冒口上方,以熱輻射方式傳出空氣中。
如果要能直接從三維複雜形狀鑄件圖檔,直接自動產生最佳化的冒口方案設計的系統:包含冒口的位置、數量、以及大小,則需要有下列相關工作需要進行:
1. 固-液界面的三維巨觀形狀,隨凝固過程的追蹤。
2. 固-液界面外,剩餘金屬液體的流動現象。
3. 以及冒口設計的準則以及自動產生冒口方案的軟體。
理論準則與設計系統
本系統之所以有別於之前的模擬軟體(CAE)或是建議系統資料庫;它是依據鑄造專家的理論,給予輸入的鑄件外型檔案,自動產生解決鑄造缺陷問題的鑄造冒口方案設計。
本系統利用數值模擬追蹤固-液界面的三維形狀的方法,來了解下列的問題:1.固液界面的移動速率和溫度梯度的關係、2.固液界面前端的液體濃度變化、3.固液界面最終隔離的熱點位置、4.由隔離熱點中,剩餘液體的體積及溫度,來計算剩餘液體的體積縮收量及其產生負壓力、5.負壓力與固液界面包覆的雜質(如:雙膜缺陷、氫氣、等等) 影響、6.以及形成的固體外殼的厚度以及其強度與負壓力的作用間的影響。上述這些問題是需要多種學門的研究和探討,而且包含:凝固理論、流體力學、電腦流體數值模擬、流體界面的追蹤法、以及凝固結構強度應力分析、等等。
1. 應用 VOF法偶合Enthalpy計算,數值模擬凝固過程中,剩餘液體的黏度及流動性;
2. 應用 VOF法偶合marker/particle粒子追蹤(Eulerian-Lagrangian運算法),追蹤固液界面移動及演化。
3. 巨觀模擬固液界面之結果,由封閉熱點之剩餘液體的體積及溫度,來計算凝固時其負壓力值。
4. 數值模擬熱點體積範圍與平衡負壓力,所需冒口大小間的關係;並建立熱點與冒口尺寸關係資料庫。
5. 平衡負壓力為基礎,建立最佳冒口設計演算法(optimised feeder algorithm);使用Vistual Basic程式碼連結CAD軟體,進行自動分析鑄件的最短補充路徑,及產生最佳冒口設計。
上述的方法中,包含建立數值模擬模組模擬凝固流體、追蹤固液界面外形、計算封閉熱點的體積縮收負壓力、建立熱點與冒口尺寸關係資料庫、以及建立冒口最佳化輔助軟體,等步驟。
開發的本系統,是選用商業用3D CAD軟體-Solidwork API 的功能編輯撰寫本輔助程式。Solidwork API可以嵌入Solidwork 3D CAD軟體,應用其本身的3D零件繪圖功能外,搭配Visual Basic程式語言撰寫”判斷冒口數量及尺寸”的巨集指令,如圖1的流程圖來編輯;其應用鑄件凝固模擬分析結果,所決定的熱點位置及數量,再與前項所建立的冒口熱點尺寸資料庫和關係方程式,自動產生最佳化三維之鑄件冒口設計。
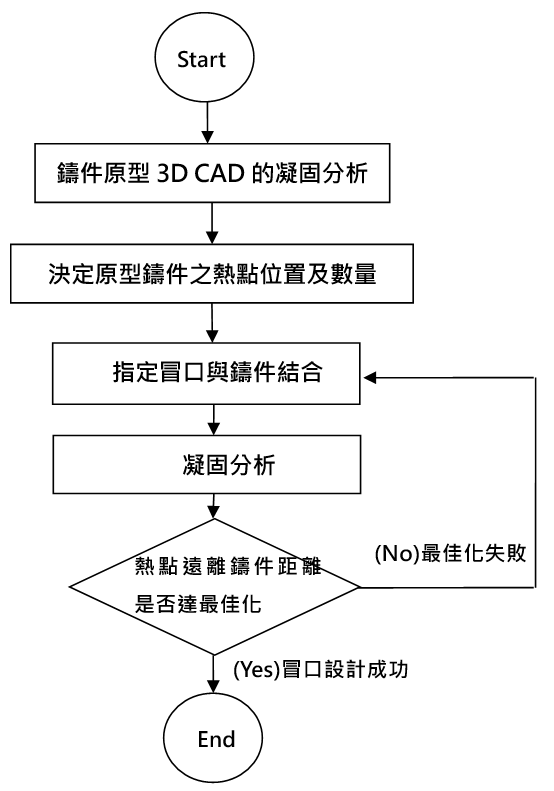
圖1自動生成最佳冒口系統(Expert System)的流程步驟
鑄件原型3D CAD的凝固分析:使用成熟的商業CFD軟體,重覆微調 (tuning) 符合實際狀況的熱物理參數,來建立數值模組,模擬凝固流體。以下用健身用壺鈴鑄件為範例,用鑄造用CAE模擬軟體(Flow 3D cast)先進行無冒口的凝固模擬,如圖2所示,確認出熱點的存在之可能縮孔缺陷現象。
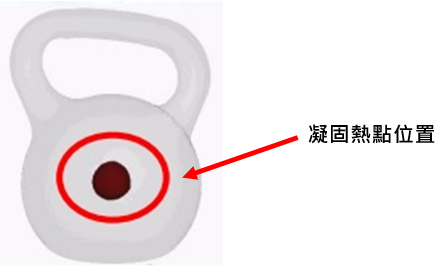
圖2 壺鈴無冒口鑄造凝固模擬熱點位置分析
更完整的內容歡迎訂購 2021年12月號 (單篇費用:參考材化所定價)
主推方案
無限下載/年 5000元
NT$5,000元
訂閱送出