- 回首頁
- 機械工業雜誌
- 歷史雜誌
摘要
金屬積層製造中的粉床式燒熔技術(Powder Bed Fusion, PBF)正以快速成長之姿,已漸漸從打樣應用到終端零件應用,在航太、模具、醫材等高值產業中嶄露頭角。然而此技術需克服急速加熱冷卻引起之熱應力所產生的殘留應力破壞問題,殘留熱應力輕則導致成品翹曲變形無法達到設計規格要求,重則可能會引起機台機構損耗、停機導致製程停擺,浪費製程材料與時間。透過工研院雷射與積層製造科技中心研發之虛擬製造技術,製造者可在長達數天或數周的製程啟動前進行虛擬製造,預視製造結果是否有風險或成品精度會否無法達到要求,協助製造者強化設計降低製程風險。此技術已開發成一獨立軟體-ITRI AMSIM,讓使用者快速得到預測結果並改善設計,可大幅減少因搭配試誤法之真實製程所造成之材料與時間成本浪費,以提高PBF設備投資報酬率。
Abstract
Powder bed fusion (PBF) is a metal additive manufacturing technology that has been rapidly applied in aerospace, molding, and medical devices manufacturing industries to produce end-use parts. However, the PBF process involves a highly localized laser heating, resulting in a large thermal gradient that induces residual thermal stress and deformation in the finished build. The excessive thermal stress in the part leads to final part fails to fit in size, or more severely, causes termination of the manufacturing process due to recoater crash issues, wasting a lot of time and cost for those failed builds. ITRI develops a virtual printing technology to predict the outcome of PBF process that spans for days to weeks in just a few hours, assisting manufacturers to visualize the possible build risks and prevent failures. ITRI AMSIM is developed based on the virtual printing technology for PBF process; it provides users to visualize the predicted outcome of the process and optimize the design for first-time-right printing. It further reduces waste of time and cost in actual manufacturing process and improves the return on investment of PBF equipment.
前言
積層製造(3D列印)近年來已逐漸從快速打樣的應用慢慢發展至終端應用商品上,其相對於傳統製造的優勢為材料可重複使用減少浪費、複雜幾何之製作成本的降低,使得此技術漸漸地可被不同產業之複雜應用使用。金屬粉床式燒熔技術(Powder Bed Fusion, PBF 或Selective Laser Melting, SLM)更是在金屬製造工業中相當受到矚目,主要原因是成型的品質與其他技術相比下更可產出較精緻成品之優勢,但其缺點則是因為要維持高精度製作使得整體製程耗時很長,加上熱應力造成成品變形與設備昂貴等問題,造成投入此技術之門檻相對高。
金屬粉床式燒熔技術是透過雷射在定厚度之粉層進行繪圖式燒熔,接著重複鋪上新粉,進行上千甚至萬層的粉體燒熔堆疊成型,也因此過程中成型工件受到千甚至萬次急速加熱冷卻過程而造成高熱應力累積,最終殘留於成品中之應力將導致翹曲變形。傳統製造流程中(如圖1上方黑虛線框),圖檔載入後將進行前處理如製程參數設定、製造方向與擺放姿態決定、抑制製程中翹曲變形之支撐結構設計與補強等等之後,才可開始實際製程,製作完成後,最終將透過逆向掃描進行成品尺寸相關品保控制。在前期缺乏經驗時開發不同材料製程相當困難,傳統透過實驗試誤法需花費三至四個月時間進行製程參數探索,相當費時與效率低下。為了解決此相關問題,工研院雷射與積層製造科技中心(以下簡稱雷射中心)針對微觀尺度與巨觀尺度分別開發雷射與粉體相互作用之多物理耦合分析模型與巨觀製程熱應力分析模型。在微觀尺度下之雷射-粉體多物理耦合分析模型主要以矯正型光滑流體力學(Corrective Smoothed Particle Method, CSPM)方法為基礎,模擬微觀尺度下雷射與粉體之相互作用,用於協助在新材料製程開發階段快速運算取得製程參數之可操作範圍,單一計算的時間相較於傳統有限元素法提升了86倍且經實驗驗證與有限元素法預測結果一致。
另一方面,在巨觀尺度下,目前PBF製作小於25公分工件的製程,一般需要數天甚至大於兩周的製作時間,然而如先前所述之熱應力損壞所形成的變形易造成成品公差不符需求或變形量過大而影響鋪粉機構進行作業導致停機,使得當次材料、人工與時間的浪費。透過試誤法的經驗累積必須在失敗過後進行支撐強化,然而若遇到製程停機失效的情況下後續製程將無從參考,製造者可能需花費3~5次試誤才可成功,成本的浪費當然也是倍數累積。為了降低學習曲線帶給製造者之困擾,工研院雷射中心以有限元素法為基礎開發之巨觀製程模擬軟體ITRI AMSIM,透過預前模擬──虛擬製造快速取得製程結果,可一次得到製程中高風險資訊協助支撐設計與強化,提高製程良率與效率。圖1左下方虛線框展示的是不同應用之模擬結果,包含GE航太用鈦合金支架與髖關節鈷鉻合金植入物,虛擬製造提供製作完成後工件變形量之分布預測協助製造者進行支撐設計強化。
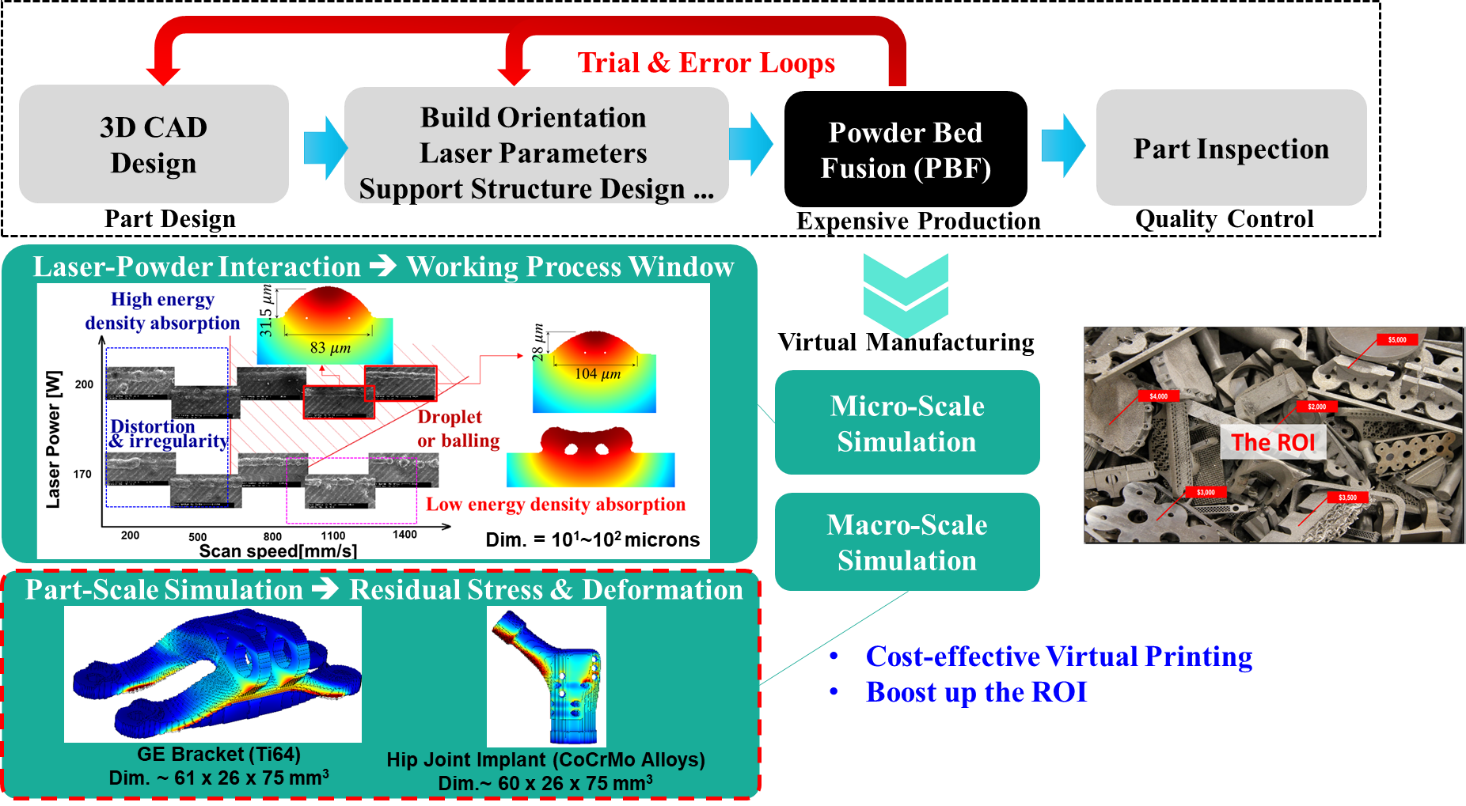
圖1 金屬粉床式燒熔製造流程與預前模擬虛擬製造流程
微觀模擬屬於新材料開發階段之虛擬製造技術,其主要目的在於為設備商或粉體材料開發商尋求新材料製程之最佳製程參數,有關上述微觀尺度下雷射與粉體之多物理耦合分析模型等相關資訊,可請參閱[1];而本文將著重介紹ITRI AMSIM巨觀製程模擬,該模型如何協助製造者在數十分鐘內完成虛擬製造,預視耗時長達數天或數周的製程結果,並透過支撐設計強化降低製程風險,達到「初次即成功」之積層製造體驗。
回文章內容列表更完整的內容歡迎訂購 2021年02月號 (單篇費用:參考材化所定價)
主推方案
無限下載/年 5000元
NT$5,000元
訂閱送出