- 回首頁
- 機械工業雜誌
- 歷史雜誌
摘要
快速切削模擬為CNC加工驗證的良好解決方案,但考量花費、機種及新舊,對廠內所有機台安裝獨立模擬設備大有困難。本文的跨平台實機虛擬化加工檢視技術,單一系統即可實現全廠各式機台的加工模擬。利用通訊介面將廠內所有機台與本文之模擬系統連結,取得各機台獨立資訊,配合以對應機台構型建置的運動鏈,模擬出在加工區內與實機高一致性的虛擬加工環境。執行NC(Numerical Control)碼即可快速檢視正確性與預估工時,並於3D畫面瀏覽加工結果、有無干涉或碰撞。接著利用M碼G碼轉換機能,轉檔為目標廠牌控制器的NC碼,將其發配至對應機型,並開始加工程序。本文技術有效消弭異個控制器品牌間的差異、降低機台硬體需求,提升總體效率並減少人力與材料耗損。
Abstract
The fast machining simulation is a good solution for CNC machining verification. Considering cost, variation of machines, new and old models, it is very difficult to install individual simulation equipment for each machine in the factory. With the cross-platform physical machine virtual processing inspection technology discussed in this paper, a single system can realize the processing simulation of various machines in the whole factory. One can simply use the communication interface to connect all machines in the factory with the simulation system mentioned in this article to obtain the individual information of each machine. The kinematic chain built in the corresponding machine’s configuration can be used to simulate a virtual environment with high consistency in the processing area. With this platorm, one can execute NC (Numerical Control) code as quick check for correctness, estimate the working hours and browse the processing results on the 3D screen for interference or collision. The M code to G code conversion function can be used to convert file into the NC code for target brand controller, distribute it to the corresponding model, and start the processing program. This technology can effectively eliminate the differences among controller brands, reduce machine hardware requirements, improve overall efficiency, and reduce manpower and material consumption.
前言
機械加工產業是台灣重要的經濟產業之一,在工件量產前,會有將NC指令進行預加工測試的程序,確認成品是否符合規格要求、加工過程是否會發生機構干涉、撞機、負載過高等情形。實機加工測試雖最為直觀,但過程中試切材料與刀具的耗損、費時都是導致成本增加的因素。隨電腦運算能力的增強,以軟體化的虛擬切削模擬來取代實機試加工,是一大幅減少材料耗損與驗證時間的有效解決方案。但因模擬設備成本考量、機台種類繁多且新舊不一等因素,若每台設備皆安裝其獨立之模擬環境,則相容性與付出成本都是達成的隱憂;硬體環境上,真實機台的刀具、對應之刀座直接人工掛載,但模擬環境的刀具、刀座卻需要靠參數設定來描述生成,而人工輸入參數,不僅費時且錯誤率高,不符合成本效益;且現行虛擬切削模擬軟體多缺乏真實機台的環境配置參數,包括刀具的鎖固偏差、胚料夾持位置差異等,以致虛實間存在不少差異;又在系統上,各家控制器廠商建立的運動控制核心對M碼、G碼指令的解譯、執行結果不盡相同,以致一組NC指令無法通用於各平台的控制器上。
因以上問題的存在,工研院智慧機械科技中心發展出一套跨平台實機虛擬化加工檢視技術,目的在於以單一一套模擬系統,即可針對全廠內的各式機台進行加工模擬測試,大幅降低模擬設備持有成本與減少模擬系統在機台間的相容性問題。筆者所屬的開發團隊在實務處理上,暫以ITRI(工研院)與FANUC兩品牌的控制器做為開發依據,並保留未來擴充任何廠牌控制器的可能性。利用RS232、TCP/IP與設備通訊函式庫作為資料傳輸途徑,將廠內所有機台控制器連結至本文之模擬系統平台,取得各機台之刀具資訊、環境參數等數值,啟用預先建立好的機台3D模型,將來自實際機台的參數與資訊匯入該虛擬機台環境,利用刀具資訊建立機台上的虛擬刀具描述,以環境參數生成欲加工的胚料並進行對刀校正,建立在加工區域內與實機高度一致的全虛擬加工環境。
完成虛擬加工環境的設置後,將欲測試的NC指令傳至模擬系統執行,即可快速檢視該程式碼的加工正確性與加工預估時間,並於3D畫面瀏覽胚料加工結果、與實機有無干涉或碰撞情形。而後利用系統內ITRI及FANUC的NC指令M碼G碼轉換表,藉由程式的自動轉換機制,達成跨控制器廠牌的NC指令相互轉化功能,最終將轉換完成的NC指令發配到與其對應的機型上,即可進行量產作業。同時系統內也保留擴展與自定義空間,廠商可自行增改M碼、G碼轉換與對應內容,並可擴充其他廠牌的平台系統轉換機制。
跨平台實機虛擬化加工檢視技術能有效消弭異控制器平台間的差異、降低機種的硬體支援度需求,提升總體效率並降低人力與材料之成本耗損,以下筆者將依模擬系統的作業流程,簡介本技術的必要關鍵模組,冀望藉由開發成果激起更多的想像與啟發,增加國內工具機全國產化之信心,也進一步帶動工具機加值軟體產業全面提升。
機台構型虛擬化建置
工具機實機全機虛擬化過程中,機台3D構型的產出是首要工作,尤其又以與加工相關區域的精確度為重。筆者所屬開發團隊利用業界常用之繪圖軟體,將機台依各組件原始幾何尺寸與組立方向繪製3D機構組件模型,並產出各組件之STL格式圖形檔案。
因現有3D繪圖引擎發展架構,畫面元素多以有限元素網格模型呈現,即由不同形態大小的三角網格,描述3D物件表面。當遇圓形、弧線、銳角等非正交直線輪廓時,則需將表面分割成更多三角網格才能描述此一物件,模擬切削時會對網格進行交疊的布林運算,決定網格後續的存在與否,大量網格將造成電腦的運算負擔,使模擬運行效能不佳、畫面卡頓,甚至造成整體系統不穩定,故需簡化構型外觀。筆者團隊發展出一套獨立的3D構型產出準則,其中基本原則如下列簡列幾項,即是:
1.以「簡單方塊」構圖,僅量避免構型中外觀存在圓弧、銳角等相對複雜的輪廓生成。
2.省略「無相對運動」構件上的複雜外形,如螺絲孔、油孔、肋板、螺牙等,甚至是將多個完全無相對運動的結構件簡化繪製成一個構件,降低總體網格數量。
3.僅繪製外觀表面看得到的結構件部分,將內部如馬達、電箱內設備等全數省略,與加工無關的構件基本也可以全數省略不繪出。
最後,利用3D引擎提供之運動鏈設定軟體,將各構件之相對運動關係建立,如移動、旋轉之方向、距離、極值、各構件載托關係(坐標系疊加)、相依構件生成位置等,並對構型輪廓與外觀顯示進行調整與修飾設定,即可完成機台構型虛擬化的前置工作。如圖1所示。
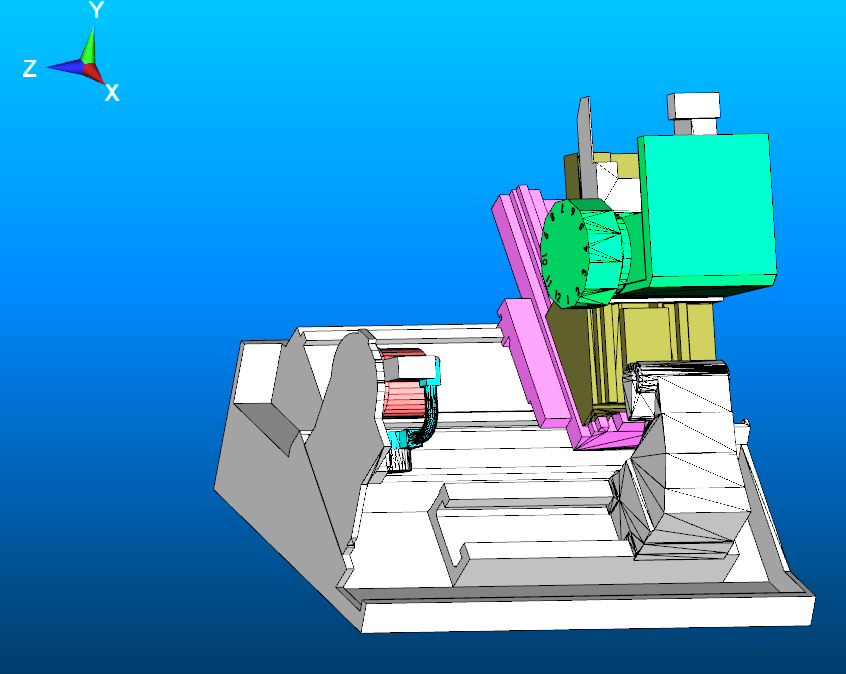
圖1 機台構型虛擬化
更完整的內容歡迎訂購 2021年03月號 (單篇費用:參考材化所定價)
主推方案
無限下載/年 5000元
NT$5,000元
訂閱送出