- 回首頁
- 機械工業雜誌
- 歷史雜誌
領袖觀點|欲數位轉型成功,不可不知的三個重點
作者 王右文、劉昀昇、陳重榮
刊登日期:2021/10/01
製造業一直存在著低毛利問題,加上五缺、經濟前景不明、需求下滑、產能下降、訂單減少等因素,經營上的挑戰越顯嚴峻。所以面對急遽變化的產業環境,「升級工業4.0」不再只是華麗名詞,已是有如上止血鉗般的當務之急,企業紛紛加速導入智慧製造及數位轉型的腳步,如圖1。
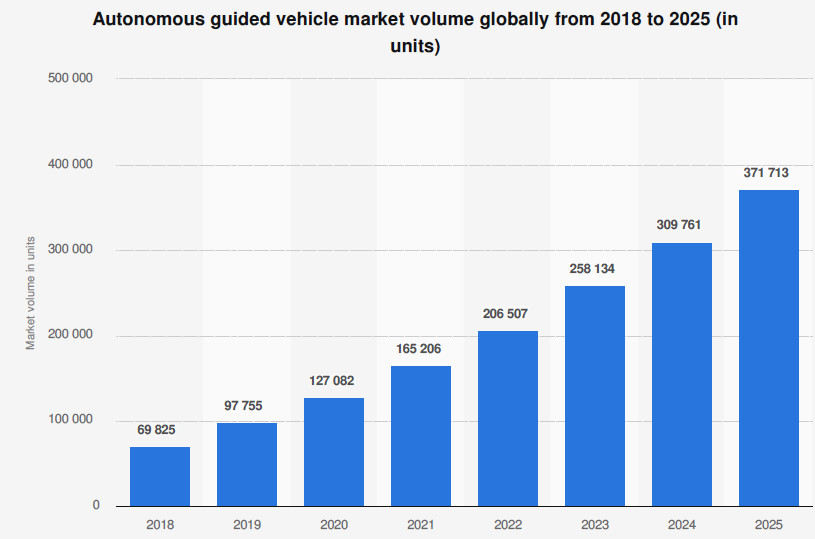
圖1 依據statista公司調查統計,AGV全球市場規模於2018~2025年間每年逐步成長
(資料來源:https://via.news/analysis/increase-automated-guided-vehicles/)
而升級智慧化工廠的策略部署當中,以導入AGV(Automated Guided Vehicle)無人搬運車的效益最為立即與顯著,除了可24小時運作,等同3位人工,亦可替代3K環境(骯髒、危險、辛苦)的人力工作,降低工安傷害,並能確實按作業計劃執行,大幅提升工廠管理的掌控度與效能,兼具涵蓋成本、人本以及管理等三大層面效益。
那麼由傳統工廠升級為智慧工廠,該從何開始著手呢?又有哪些部分值得注意呢?在此,統整了規劃自動化流程時需關注的三項重點,分述如下:
(1)自動導引方式需有彈性,廠房規劃因訂單或作業流程會有不同的變動,因此導引方式不可一成不變,必須保有彈性,能有依照需求彈性調整的空間。
(2)需考量軟、硬體整合,因應功能與環境採用不同功能特性的AGV,並將AGV與設備機台進行精密的設計與協作整合應用,將工廠內繁複、耗時、半成品、成品的物料搬運流程重新規劃,達到全自動化生產的目標。
(3)派車管理系統必須能依據需求調整修改,優秀的派車管理系統,能將車輛派遣最佳化,縮短貨物搬運時間,可確實降低營運成本、提高生產效益,是影響搬運效能的重要關鍵。
事實上,無人搬運車並不是一個新的概念,20多年前即普遍運用於半導體及面板產業,早期業界AGV多採用2D code導引方式,隨著科技的進步,為了滿足彈性路線規劃需求,新型AGV無人搬運車採用LiDAR光達+SLAM定位,與自動駕駛車相同技術的光達導引(LiDAR),加上同步定位與構建地圖(SLAM)系統,賦予主導智慧機器人感知與行動關鍵因素的自主定位導航技術,可對周圍環境進行分析、判斷和選擇,對於AGV運行路徑的建置更具效率與彈性,非傳統貼附地面的磁帶固定路徑方式可比擬。
除了導引方式多種之外,AGV亦有許多不同機型,例如:板車型、多功能型、堆高機型、窄巷型堆高機等。在針對不同的需求及應用環境時,有不同種類的AGV可適合選擇。多種型態的AGV,包含人駕堆高機在內的多機種共同協作,能全面對應不同工廠的運作需求,支援工廠內的多種載具以及輸送站與站間的運搬型式,如輸送帶、機器手臂Robot,並可與電梯、餐梯、自動門等系統整合,搬運不同類型的載具,如卡匣、棧板、通箱及Tray盤等,串接製造執行系統(MES)及設備連線,達到無障礙的無人搬運及人機協作環境,完成工廠內不同區域及跨樓層間的無障礙運輸,大幅提升工廠管理的掌控度與效能,並能進一步實現無人化、提升效率、降低成本的目標。
良好的派車管理系統,必須包含資訊整合介面的Web或APP系統,可完整掌握靈活調度,同時彈性運用便於管理。為了達到以上目的,有經驗的系統整合公司,特別將AGV的管理權限,分為作業者、維護者、管理者三種角色,依據不同角色賦予不同的管理系統。作業者使用DCS,管理者使用VMS的CFM/RPT模組,即時監控及歷史統計報表。智慧搬運APP則提供維AGV護者專屬使用,功能包括AGV車輛資訊、作業地圖、Memo紀錄、手動復歸、保修幫手等,維護者則可隨時掌握AGV車輛資訊與路徑地圖,一旦AGV發生異常時,可以依據現場的狀況,自行切換為手動功能進行操作,透過專屬APP直接操控AGV,快速達到排除異常的要求。
以實際客戶為例,某製造大廠,預計規劃24小時全天候生產流程,進行整廠自動化的規劃與升級。導入時需解決走道空間不足、連線訊號常受干擾等問題,整技科技特別規劃採用窄巷高層型AGV無人搬運車,AGV於走道約兩米空間仍可運轉作業,不需調整料架間距,以料架加窄巷高層堆高機的解決方案,達到了如同立體自動倉庫的效果,導入經費節省了50%、產能利用率提升25%,成效卓著。另外規劃各車型AGV在同區域共用一套電子地圖系統,並開發出全台唯一的「斷線續行」功能,讓AGV無人搬運車在斷線情況下,不會立即停擺,斷線後也能持續完成當下搬送命令與任務,搭配整技科技AGV智慧管理專屬APP,讓維護者可自行操作手/自動切換控制與定位測試,徹底解決訊號干擾問題,讓客戶可快速排除AGV異常狀況與輕鬆維護。
更完整的內容歡迎訂購 2021年10月號 (單篇費用:參考材化所定價)
主推方案
無限下載/年 5000元
NT$5,000元
訂閱送出