- 回首頁
- 機械工業雜誌
- 歷史雜誌
不同材質零件之組合交界線3D 軌跡提取技術應用於鞋業自動化製造
作者 黃成凱、許秉澄、陳祉翔、陳俊皓
刊登日期:2021/03/01
摘要
產業朝向智慧製造發展,執行重複動作之現場人員未來將徹底被智慧機器取代。對於金屬業以外之產業而言,各零件之加工結果容易受到加工條件因素或材料特殊性質等影響而使得尺寸變異量大,很難建立準確的加工軌跡,難以導入標準自動化流程。本文提供一種建立組合件之交界軌跡的系統,有助於正確的建立組合件的交界軌跡,可正確的建立組合件的交界軌跡以提升組合件之加工工序的製程良率。
Abstract
As industry progresses toward intelligent production and developments, on-site workers that performing repetitive tasks will be replaced by intelligent machines. The dimensions of work-piece for industries other than metal processing can be easily affected by factors such as processing conditions or special properties of materials. Therefore, it is difficult to establish an accurate processing trajectory for automation. This paper proposes a junction trace determination system for different materials assembly; it can be used for generating processing trajectory for automation and increase the yield rate.
前言
隨著自動化生產的發展,機械手臂在工業領域應用愈趨廣泛(根據國際機器人聯盟IFR統計,2019年全球機器人使用量將達272.2萬台,如圖1所示[1]),大大提升了工業生產的效率與品質。在利用機械手臂執行自動化的技術領域中,一般是將工具直接安裝於機械手臂,並透過人工教導的方式產生機械手臂動作以達成自動化應用;但人工教導等離線編程方式所產生的加工路徑為預先產生的固定軌跡,若刀具發生磨耗而造成長度改變、工件位置發生偏移或工件尺寸存在較大變異等情形發生,則加工時刀具與工件之相對關係將偏離原先之設定,而無法達到預期的加工結果,因此若工件尺寸變異量較大時,則須針對各工件分別進行軌跡識別才可執行加工。
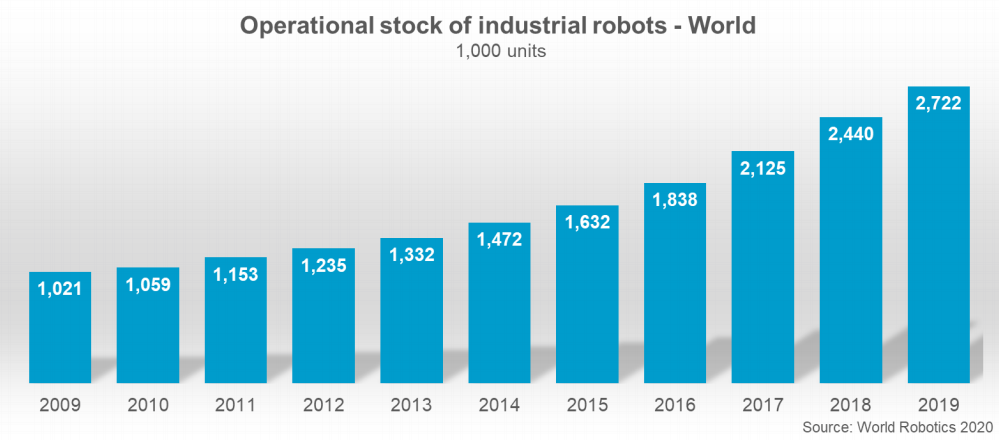
圖1 2019年機器人使用量統計
以民生工業中鞋業製造而言,全球年產值達4000億美元,且以每年20%的速度不斷成長,雖然其符合3D之製造特性(如塗膠製程為有毒物質),但目前卻都還是以大量人力製造為主,其原因為製鞋尺寸公差變異大,因此難以透過傳統的標準化、自動化流程進行加工。雖然近年來各品牌大廠希望透過自動化取代大量人力,但卻面臨良率不佳、製造流程不順,使得產能無法提升;其根本原因在於鞋業製造中,除了款式、材質、尺寸眾多以外,還受到加工治具精度不佳(如精密鞋楦之公差約1mm)、鞋面縫製尺寸變異量大、鞋底為軟質材料易變形,因此自動化過程中無法透過標準加工軌跡來執行,而須對每一雙鞋分別產生軌跡才可進行後續加工,故欲將鞋業導入自動化首先須解決軌跡辨識之問題。
製鞋流程中鞋子並非為一體成形,而是將鞋面與鞋底分開製造;個別完成後將其假組找出結合線,針對結合線以下之位置進行打粗、塗膠等加工,以將鞋底黏合至鞋面。由於每一個鞋面縫製皆存在尺寸變異,因此結合時需視鞋面狀況調整壓合力道;為使穿著舒適,鞋底多為軟性材質所製,壓合後會發生變形而造成每一雙鞋之結合模線位置皆不相同,因此結合模線識別之正確性直接影響加工結果。
以自動化設備執行鞋面打粗、塗膠等動作,首先須先確認結合模線之位置,但由於尺寸變異、壓合變形等皆會存在誤差而無法正確取得軌跡資訊;雖然目前有一些方法可以找到加工軌跡,但卻都存在一些問題而無法準確、快速完成辨識,現有方法具有以下缺點:(1)透過背光板使工件與背景有明顯色差,以辨識外型輪廓,但對於鞋業而言,由於結合模線並非為外型輪廓位置因此無法準確辨識[2];(2)透過點雲識別產生軌跡:此方法用於鞋面結合線之辨識時,由於底模為軟性材料,故結合前後之外型尺寸不會完全相同[3][4][5],因此點雲識別所得之軌跡與實際結合模線存在一些誤差而無法準確辨識;(3)透過慣量感測器分析裝置軌跡以轉換為三維資訊:此方法受限於擷取速度與慣量感測器之精度,使得繪製過程中僅能慢速繪製以避免擷取過多雜訊而使軌跡誤差過大[6]。
鑒於以上問題,本文提出組合件交界線3D軌跡提取技術,透過3D點雲模型比對技術,此技術首先對各零件分別建模,當零件組合後即可透過點雲模型比對之方式比對各零件於組合件之位置,接著再透過材質檢測分析儀器搜尋異材結合之交界位置;以鞋業而言,此技術首先對底模與鞋面建模,當兩者組合後,即可透過3D點雲比對之方法,搜尋底模於組合件上之位置,找到模口線之可能區間,接著再透過材質分析器於區間內分別對材料進行檢測,使其激發材料特徵,根據此特徵值判斷是否為相同材質,故可透過此方法搜尋底模與鞋面之交界線完成鞋面自動化加工之軌跡辨識,解決現有方法受到材質/顏色影響、資料擷取頻率低且包含大量雜訊,或軟質材料壓合變形後無法正確評估軌跡等問題,如圖2所示。
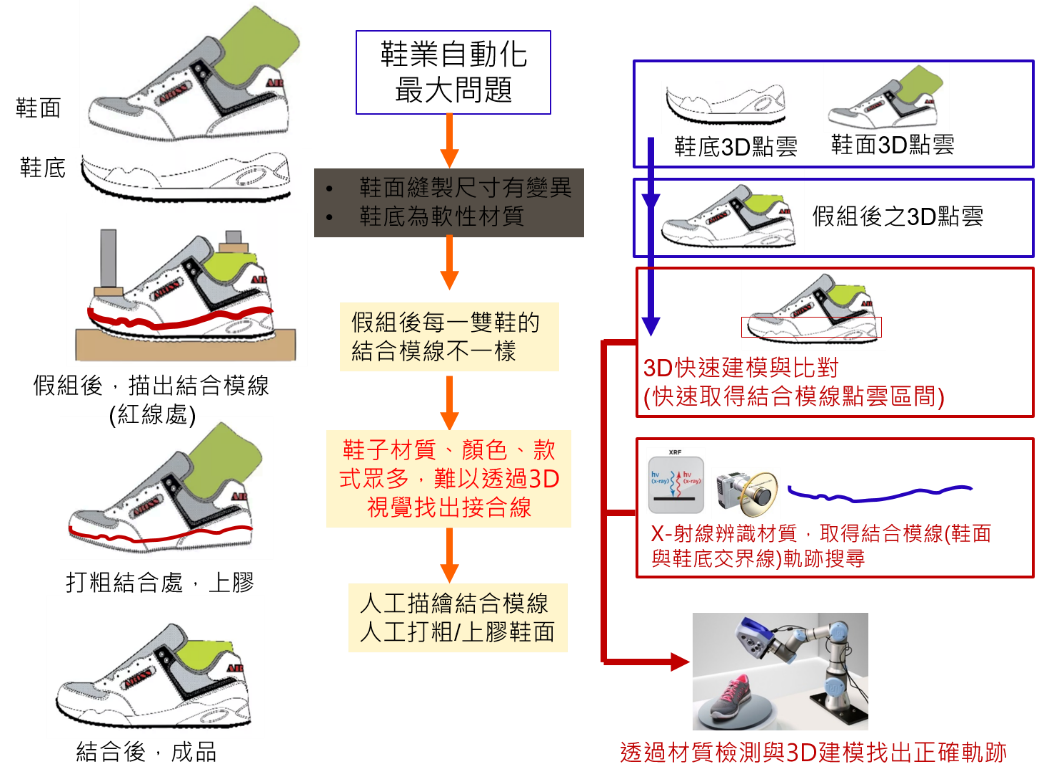
圖2 3D軌跡提取技術流程圖與鞋業製造問題
異材結合交界線3D軌跡提取方法
鞋業製造中,要將鞋底與鞋面結合首先須先將其假組,找出組合之結合模線後,在針對鞋面之結合線以下進行打粗、塗膠等加工流程後才能將其保持結合,但因為鞋面布縫製尺寸存在許多變異因素,且鞋底為軟質材料,使得假組後每一雙鞋之結合模線皆不相同,因此目前都還是以人工描繪結合模線,再進行後續的人工打粗、人工上膠等製程。但對於鞋業打粗、上膠等製程存在許多有毒物質,且加工品質受到操作者的經驗與技術影響,使得良率難以有效提升。本文提出異材結合交界線3D軌跡提取技術,以此方法提取鞋底與鞋面之結合模線,即可將軌跡資訊數位化透過自動化設備進行後續製程,以下將針對3D軌跡提取技術進行詳細說明
更完整的內容歡迎訂購 2021年03月號 (單篇費用:參考材化所定價)
主推方案
無限下載/年 5000元
NT$5,000元
訂閱送出