- 回首頁
- 機械工業雜誌
- 歷史雜誌
摘要:伺服沖床相較於傳統沖床的最大特徵,在於能夠控制沖頭的運動及速度,並配合不同的加工目的,使用最適合之成型曲線,以達到最大的生產效率。對於伺服成型曲線智慧化,必須先拆解其特性。曲線分為有加工與無加工,其中有加工部分需要根據需求使用不同的曲線,有不同的曲線後,可以再拆解曲線中每個轉折節點,也就是智慧化需要對每個節點進行判斷,並選擇最好的路徑。因環境議題使鋁合金採用率上升,而7系列鋁種之鈑金因強度高延展性很低,成型時易破裂,因此成品品質不佳造成量產難度高,愈加顯示伺服沖床成型曲線智慧化工具的重要性以及未來市場發展潛力。
Abstract:The most important feature of servo press compared to conventional press is that it can control the movement and speed of the punch and use the most suitable forming curve for different processing purposes to achieve the maximum production efficiency. In order to achieve the maximum production efficiency, the most suitable forming curve must to be used for different processing purposes. The curve can be divided into processed and unprocessed, among which the processed part needs to use different curves according to the demand. After divided into different curves, each turning node in the curve can be disassembled, which means to be intelligent it needs to judge each node and choose the best path. Due to environmental protection issues, the adoption rate of aluminum alloy is increasing, but the 7 series aluminum sheet metal is easy to break during forming process due to its high strength and low ductility and the quality of finished products will be affected and difficult in mass production, hence the importance of intelligent tool for forming curves of servo punch press and the potential for future market development are increasingly demonstrated.
關鍵詞:伺服沖床、成型曲線、金屬成型
Keywords:Servo press, Forming curve, Metal forming
前言
鈑金成型的應用已經有大約6000年的歷史。雖然沖床的歷史可以追溯到很久之前,但沖床的演變卻非常緩慢。公元前600年,Greco首次使用壓榨技術從橄欖中提取油。後來,Heron of Alexandria 在他的書中提出了第一個螺旋式壓榨機的想法。最早應用於金屬鈑之操作軋機為分切機,1590年從比利時到英國都在使用。液壓機作為一種可控的金屬成型工作台是由英國科學家Joseph Bramah在1795年建造的。後來,液壓機配備了電動馬達,以完成所需的壓力。
沖床的演變隨著其運動機制改進而完成,對沖床的研究在19世紀和20世紀之間得到了迅速的加強。在過去的40年裡,這種沖床的滑動運動和驅動機制沒有顯示出明顯的進步。在20世紀60年代,在歐洲和美國科學家的技術合作下,引入了連桿運動機構。在今天的工業基礎上,用模具和沖床進行金屬板加工是生產金屬板部件的最有利的製造系統之一。
鈑金成型涉及各種綜合技術。這種操作面臨著一些困難,如高強度和低延展性材料的成型,對高精度的要求,生產力的提高,以及對低能耗的評估。伺服沖床與傳統的沖床相比,它具有顯著的特點,即改善工具壽命、加工精度、提高生產率、減少噪音和振動、低能耗和短加工時間。伺服沖床的使用已被證明對難以成型的材料是成功的,如高強度鋼、鋁合金和鎂合金[1]。
伺服沖床核心技術
伺服控制技術在近二、三十年已廣泛地應用在一般工具機與自動化設備上。近年來國際間3C與光電產業對於沖鍛零件之產品淘汰率越來越快,形狀越來越複雜,加工道次卻要求越少越好,進而提升產能並降低成本。因此從1990年初開始,日本幾家沖床製造廠便推出以伺服馬達為驅動源之伺服沖床,藉由伺服馬達高自由度的控制機制,產生多變的滑塊運動曲線,以因應目前多樣化及零件形狀複雜化的製造趨勢[2]。
傳統沖床與伺服沖床結構差異如圖1所示。傳統機械沖床中的電機是通過飛輪、離合器和制動器安裝在小齒輪上。在伺服沖床中,電機可以是直接安裝在小齒輪上,因為伺服電機是能在任何點提供任何扭矩,意即現有機械沖床的結構(即螺桿,曲柄,連桿,和轉向節)在伺服沖床中得到加強。伺服沖床從技術角度來看具有幾個優點 : 沖床具有程序的沖程,以便它們可以掌握在任何速度和行程中的任何點,生產效率高於傳統液壓機和傳統機械沖床,差異處如圖2所示。此外,傳統沖床使用飛輪儲存能量,於需要時釋放。雖然這樣的設計可使用功率較小的馬達,但沖床在非加工狀態下,仍須保持飛輪空轉,能量仍然持續消耗 ; 反觀伺服沖床可設定只在加工段產生所需之出力,在非加工段則可將動力輸出節省起來,且無飛輪空轉之狀況。因此比起傳統沖床,伺服沖床更加節能減碳符合未來趨勢。
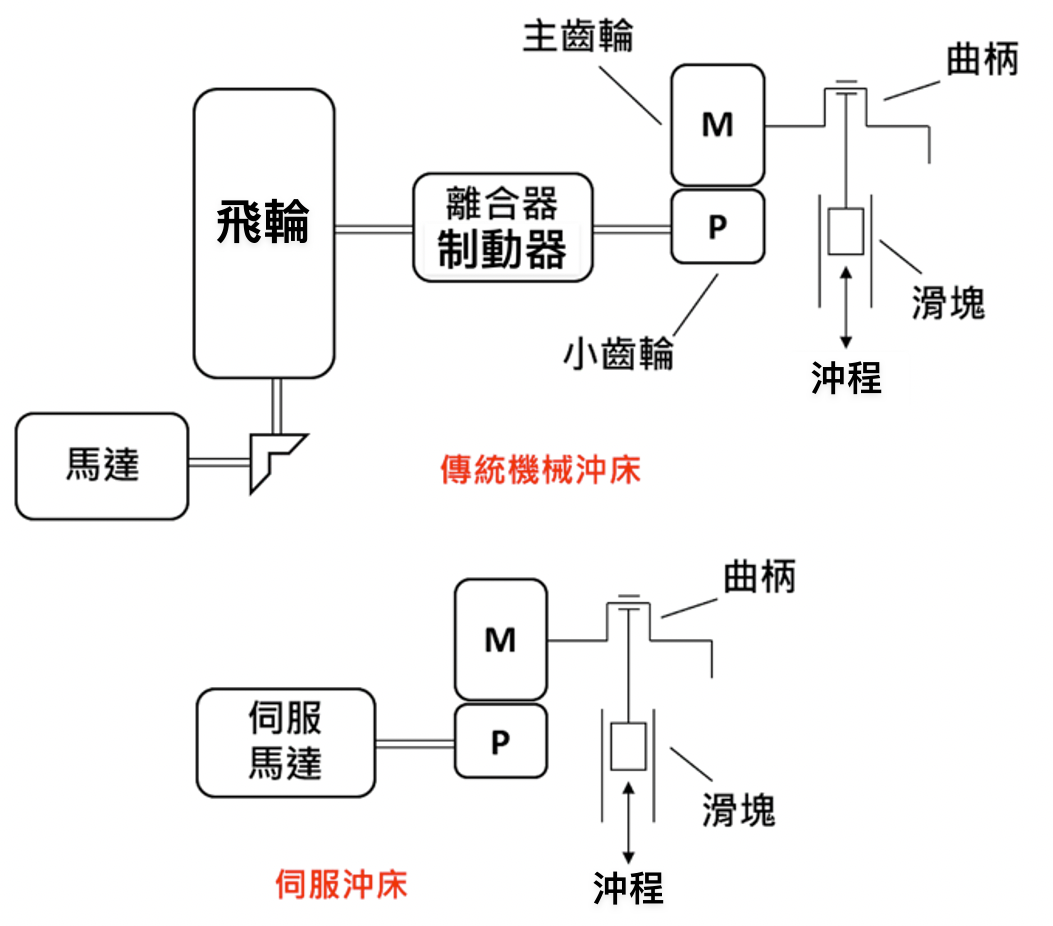
圖1 傳統沖床與伺服沖床結構差異
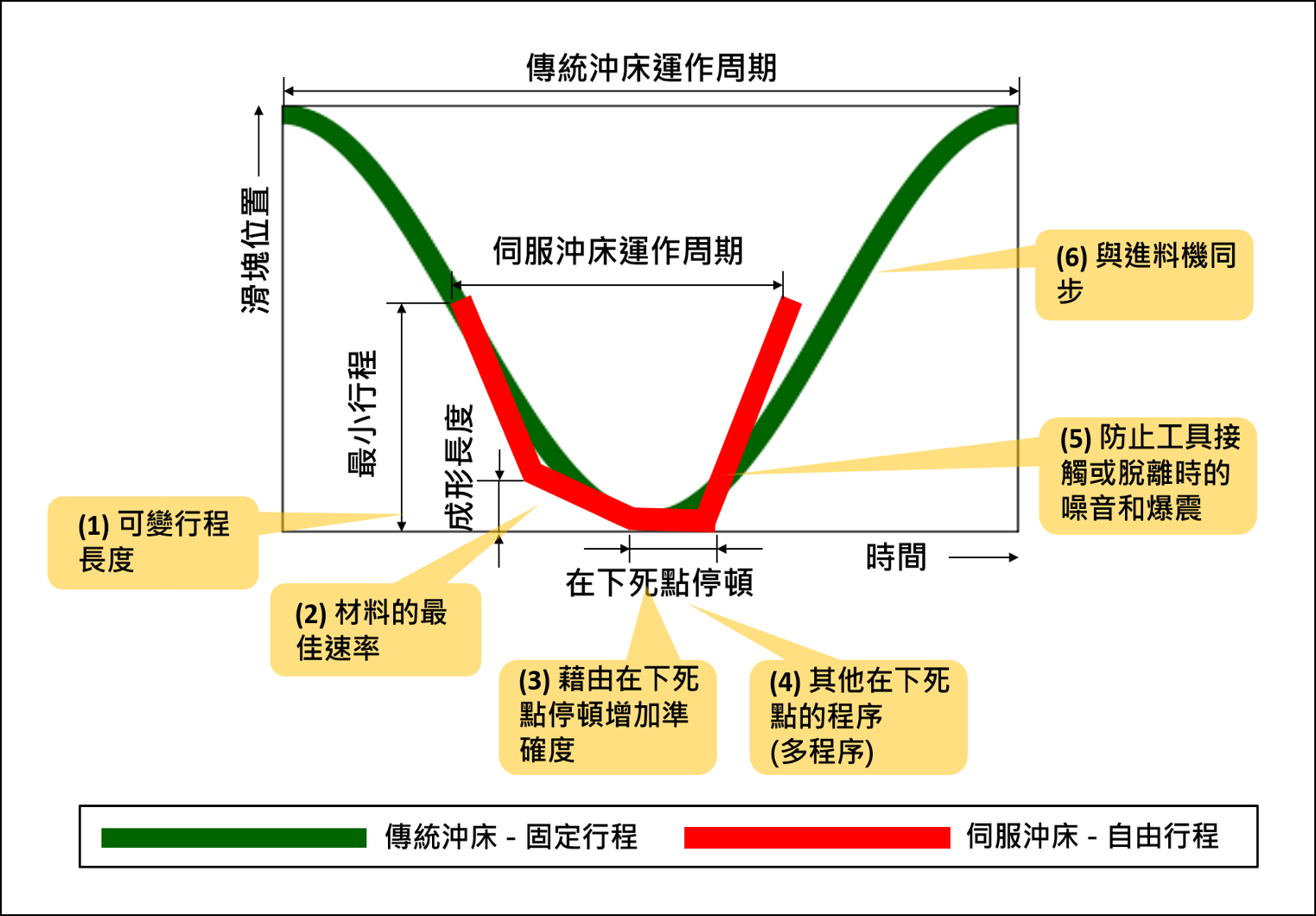
圖2 伺服沖床與傳統沖床差異
回文章內容列表更完整的內容歡迎訂購 2022年05月號 (單篇費用:參考材化所定價)