- 回首頁
- 機械工業雜誌
- 歷史雜誌
高附著性玻璃金屬化之濕式製程技術
作者 王偉彥、張佑祥、黃萌祺
刊登日期:2022/06/01
摘要:玻璃基材是一具有潛力能夠取代矽應用於中介層的材料,因其具備低介電常數與可調式熱膨脹係數,另外製作成本相較於矽低廉且無尺寸上的限制,然而玻璃基材與銅層存在附著性不佳之問題,導致玻璃基材遲遲未被廣泛應用於中介層上。為解決此一難題,本文開發一高附著性玻璃金屬化之濕式製程技術,藉由獨創合成塗料於玻璃上塗佈一附著層並結合濕式金屬化技術,最終玻璃與銅層附著力達到約452 gf/cm,近乎於商用附著力標準值,此外,本技術也可應用於高深寬比的通孔玻璃中,並且達到均勻且連續的金屬鍍膜。
Abstract:With properties of low dielectric constant and adjustable thermal expansion coefficient, the glass substrate is a material that has the potential to replace silicon for interposers. In addition, the production cost of glass substrate is lower than that of silicon and there is no size limitation. However, the adhesion between the glass substrate and the copper layer is poor, resulting in the glass substrate not being widely used on the interposer. In order to solve this problem, a novel wet-process technology for high adhesion glass metallization is developed. By coating an adhesion layer on the glass with the distinctive synthetic paint and combining with wet-process metallization technology, the adhesion values between glass substrate and copper layer reaches about 452 gf/cm, this is close to the standard value of commercial one. In addition, this technology can also be applied to high aspect ratio through-hole glass and achieve uniform and continuous metal coating.
關鍵詞:玻璃、金屬化、中介層、化學鍍、附著力
Keywords:Glass, Metallization, Interposer, Electroless plating, Adhesion
前言
隨著半導體技術快速發展,電子產品裝置尺寸從先前數十微米縮小至幾十奈米,甚至是幾個奈米的規格,莫爾定律的應用漸漸走入極限,為了能讓超大型積體電路(Very Large Scale Integration, VLSI)元件達到高效性能的表現,在封裝技術的成長也從早期的打線封裝(Wire bonding)演進至覆晶封裝(Flip Chip),再逐漸到現今較新的系統單封裝技術設計(System in Package, SiP),所謂的SiP封裝技術就是將數個不同功能的晶片整合在共同基板上,再由基板將不同元件合併連接,根據SiP封裝設計又可細分為2.5D封裝和3D封裝兩種三維封裝技術[1]。此三維封裝技術主要是解決基板在佈線密度上的問題,由於採用基板垂直通孔的方式是將晶片與載板互連,有效縮短互連導線的長度以及減少訊號傳遞時的延遲與損失,而晶片與載板間通常存在一非導體連接基板,稱為中介層(Interposer)[2],如圖1所示。
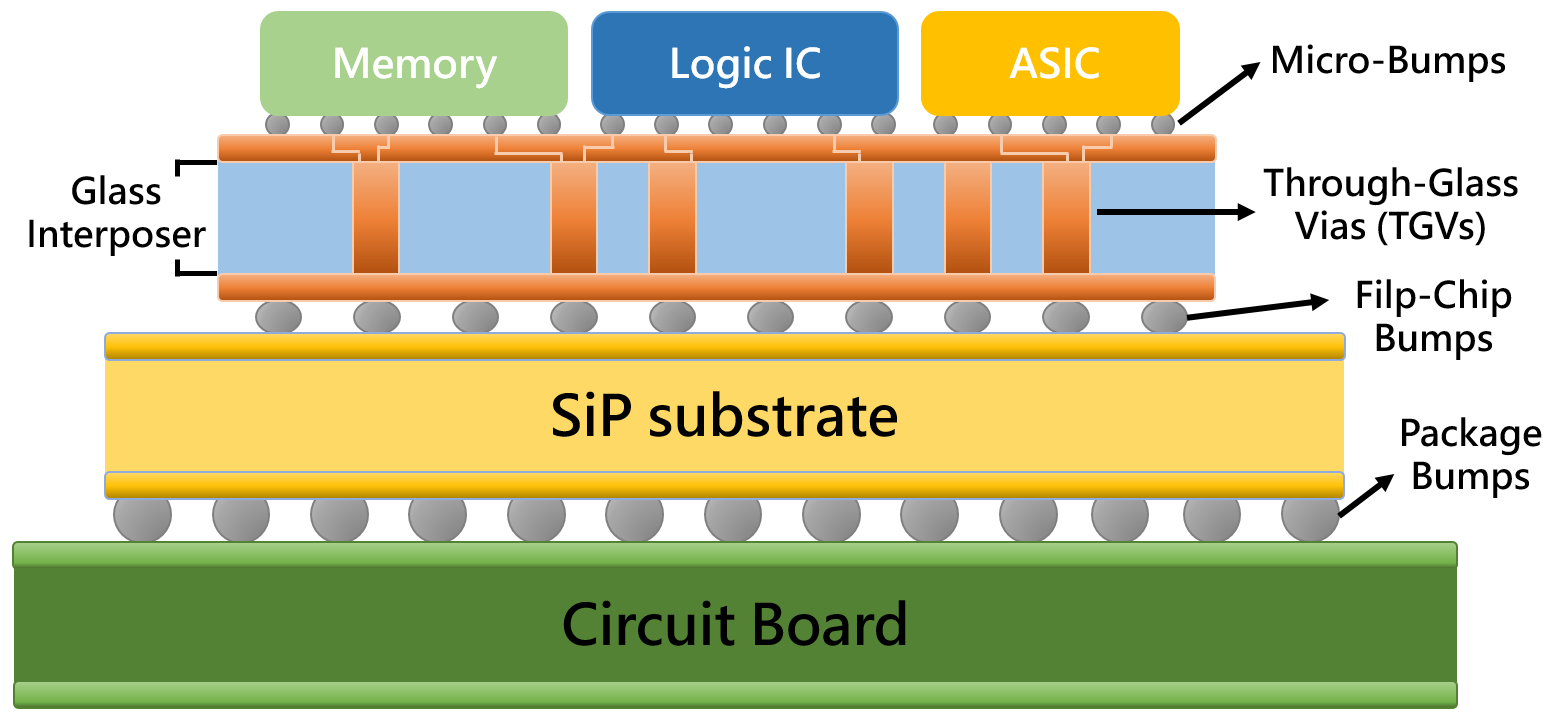
圖1 中介層示意圖
中介層材料早期的應用多以陶瓷、有機或是聚合材料為主[3],然而隨著線路設計的微小化趨勢,這些較高介電常數(Dielectric Constant)的材料在訊號的延遲與損失上變得越來越嚴重,再加上小尺寸規格穩定性差及多層堆疊時易出現基板翹曲等問題,故後來的發展以矽作為中介層材料。雖然矽有較低的介電常數,但後續加工成本較高且尺寸的規格受限於晶圓的大小而難以達到大面積的應用[4-5],因此近年來眾多研究團隊嘗試採用玻璃來替代矽作為中介層材料的應用。玻璃相對於矽晶有更低的介電常數,且熱膨脹係數 (Coefficient of Thermal Expansion, CTE) 也與矽晶相近,再加上大面積玻璃基板取得容易且製作成本低和尺寸穩定性佳等諸多於矽晶的優點,使玻璃成為未來替代矽作為中介層材料之首選[6]。
玻璃金屬化方式
雖然玻璃有眾多作為中介層材料的優點,但目前玻璃應用於中介層之導電線路製作的技術並非如預期中廣泛,源於玻璃金屬化技術有許多艱難的問題待突破,其中又以金屬與玻璃間附著力不佳的議題最為棘手,倘若能突破且提升玻璃金屬化技術的成熟性及穩定度,必能縮短玻璃應用於中介層之期程。目前玻璃金屬化的方式大致可分類為乾式及濕式兩種技術,其中乾式技術又以物理氣相沉積 (Physical Vapor Deposition, PVD) 為主[7],如真空蒸鍍沉積 (Vacuum evaporative PVD) 、濺鍍沉積 (Sputtering PVD) 和離子鍍沉積 (Ionic Plating PVD),濕式則是以化學鍍沉積技術為主。
乾式物理氣相沉積技術是指在真空環境下利用物理方式將金屬靶材氣化成原子、分子或是部分離子態,而後經過低壓氣體或是等離子體在待鍍物表面沉積薄膜材料的方式,以真空蒸鍍沉積來說,其製作方式就是通過物理加熱蒸發的方法將欲鍍材料氣化後,於待鍍物表面沉積薄膜,其薄膜厚度可藉由控制蒸發速率及沉積時間來調控,在日常生活中所使用的鏡子就是以此方式製作而成。而濺鍍沉積技術又名陰極濺射法,其原理是在真空環境施加電壓產生電場,而在此電場下通入惰性氣體(如氬氣),藉由惰性氣體形成高能粒子來轟擊金屬靶材,使其形成微粒子團濺出並沉積於待鍍物表面,濺鍍沉積技術的好處在鍍層厚度較低的情況下能有良好的附著性,且鍍層應力也相對較低,此外在不破壞原有系統下可透過改變靶材料沉積不同的薄膜,然而濺鍍靶材的利用率僅不到五成,再加上析鍍速率相當慢,導致製作薄膜的成本相對較高。最後離子鍍沉積技術,其整合蒸鍍及濺鍍技術將蒸發物質分子以等離子體電離技術使其離子化並沉積在待鍍物表面,雖然離子鍍具備高沉積速率及優良的鍍膜附著性,但其缺點在於待鍍物需具備導電性且鍍膜過程待鍍物的溫度會升高至幾百度,因此應用範圍受到很大的限制。
回文章內容列表更完整的內容歡迎訂購 2022年06月號 (單篇費用:參考材化所定價)
主推方案
無限下載/年 5000元
NT$5,000元
訂閱送出