- 回首頁
- 機械工業雜誌
- 歷史雜誌
摘要:近年來為了因應全球化生產,產品開發週期縮短,業者須具備快速反應能力以獲得國際訂單,快速試作技術因此興起。透過數位路徑控制以及減少專用模具使用且可於短時間內生產部件的漸進成形技術為目前國際於相關成形技術的發展趨勢。本文以一深引伸零件作為漸進成形試驗載具,首先透過成形路徑設計及製程參數建立CAE分析模型,並進行成形道次規劃。而後於金屬中心建置之漸進成形試作場域以機械手臂進行實際試作驗證,並將CAE分析結果於成形之鈑件進行比對,結果顯示透過漸進成形CAE分析進行路徑及成形道次規劃可提升成形後鈑件品質。
Abstract:In recent year, to adapt to globalization for shortened lead time and expedited reaction to product development, the manufacturers have to adjust themselves to develop rapid prototyping techniques in order to attract international demand. Incremental forming technology, which manufactures products in a short time with digital path control and reduced number of forming tools, has become the current development trend in global prototyping technology. A deep drawing part is formed by incremental forming process in this article. The forming steps is first designed through the CAE model established through forming tools path design and process parameters. Then, the incremental forming process is carried out with robot in the forming lab built up by MIRDC. And the formed parts are compared with the CAE analysis. It shows that the formed parts quality of incremental forming can be improved through the path and forming steps designed with CAE analysis.
關鍵詞:板金漸進成形、快速試作、數位化控制
Keywords:Incremental sheet forming, Rapid prototyping, Digital control
前言
因應全球化生產,產品開發週期縮短。為滿足此需求,須具備快速反應能力以獲得國際訂單,導致模具製造週期縮短,國內廠商需可小批量且低成本的製程以提供客戶高品質試作件,才具備搶單競爭能力;除此之外,因應少量多樣市場,品牌廠每年均需新產品、新零件開發,產品試作費用逐年成長。目前各產業包含塑膠製品、金屬製品,板金、塊材等不同形式的產品多以RP (Rapid Prototype)技術,直接列印或機械加工製造產品,通常可在一周內完成所需產品形狀,但在提交樣品數量多的情況(如>20件),直接製作或以3D列印的方式來進行產品開發成本過高,目前國內有採用快速模具RT (Rapid Tooling),利用可快速加工的樹脂模具或快削鋼設計簡易的模具結構進行小批量試打樣,或以砂模3D列印配合可回收之鋅合金鑄造模來降低試作模具成本,與直接打樣相比雖可降低小批量試製成本,但生產時程亦會提升。
面對未來消費者對客製化需求日益增長的趨勢,針對薄板部件少量製作需求,國際上目前已發展特殊成形工法如彈性化多點模具成形(Flexible Multi-point Plate Metal Forming Technology),彈性化旋壓成形(Flexible Spinning Forming Technology),及目前發展最久且已應用於多種板金零件試作的板金漸進成形技術(Incremental Sheet Metal Forming Technology)。彈性化多點模具成形技術是將傳統模具的整體表面離散化成一系列高度可控、排列規則的沖床矩陣。每個離散點是一個獨立的移動單元,透過控制每個點的相對垂直高度來改變成形面的形狀,沖頭矩陣形成的包絡面是所需的成形面,無需更換模具即可藉由控制各點的位置快速成形,各種不同複雜形狀的曲面產品,國際上已應用於多個領域,包括高速列車車頭罩、汽車罩、船舶外板等大型板金產品。傳統旋壓將材料快速軸向旋轉,成形輥頭類似車床靠近旋轉工件,使工件產生軸對稱變形。而彈性化旋壓成形為傳統旋壓成形再加上多軸的控制藉此增加成形自由度,可利用數值控制成形出非軸對稱的旋轉體薄壁零件,旋壓所獲得的產品精度也相對較高,品質更好,國際上已廣泛用於航太、軍事、核能等金屬精密加工領域[1]。
漸進成形技術同樣利用數值控制的方式,藉由CNC或機械手臂等硬體設施依路徑控制輥頭模具,將夾持在夾治具上的平板依序做塑性的變形,逐步變形成最終的產品形狀。漸進成形技術有許多不同的種類,分別有單點、雙點、多點的模式,成形的方向是正向或負向的方式。
上述多以數值控制的方式進行成形加工,因可大幅減少傳統製程中的專用模具使用數量,減少模具的成本與加工時程,且能有效的提供在產品試作開發期快速對應設計變更,或因應小批量生產需求的產業而不需攤提大型的模具成本。本文將針對金屬中心目前應用漸進成形技術於板金件試作的初步研究成果進行探討。
漸進成形製程道次及參數設計
漸進成形技術成形性受到許多參數的影響,包含輥頭直徑、進給量、輥頭轉速、板材與輥頭之間的摩擦以及成形的壁角,也就是成形面與水平的夾角。其中,成形壁角受到產品形狀限制,較難從成形參數中隨意調整而改變。而金屬下料板的厚度在漸進成形中受到成形產品的角度影響很大,當成形角度超過材料的最大成形角度後就會產生破裂,國際上許多學者經過試驗發現,成形極限與材料厚度都與成形角度有密切的關係。成形極限為板金成形過程中用來判斷成形是否破裂的衡量標準,因目前尚未建立對應漸進成形之破壞模式判斷準則,因此透過厚度與成形角的評估預測成形狀態。漸進成形的過程中,材料的厚度遵循正弦定律,如下式(1),變形後的板料厚度ti是成形角Φ與初始板料厚度的函數。板料厚度在成形輥頭施加剪切力下逐漸變薄,由於輥頭相對產品的面積是相當小的,因此每點的變形對未變形區域的影響非常小甚至不影響[2]。
(1)
國際學者也針對不同材料研究單次的最大成形角,大部分材料的最大成形角多介於60~70°,以軟鋼為例,其最大成形角約65°。當產品特徵超過最大成形角則必須透過多道次的路徑道次規劃,例如90°的引伸產品,可利用中間道次使成形角度在40°~50°再進行中間道次造型的設計使材料的應變較平均的分配於各位置,避免局部位置的變形、減薄;或搭配引伸的方式,讓成形的過程中可以藉由成形區外的材料來補足成形區中的材料減薄,在實際上可藉由夾持的方式來實現[3-4]。
CAE分析模型建立
本文利用Yaskawa 600 kg六軸機械手臂進行漸進成形試驗,初期建立漸進成形CAE分析技術,與沖壓成形分析最大的不同在於漸進成形製程中需考量輥頭路徑的作動方式。因輥頭作動成形方式為隨著時間進行各方向的移動,因此其作動條件上需藉由路徑的離散化來達成。可以利用Mastercam或Visual Mesh等軟體進行路徑的離散化,如圖1(a)為我們欲進行成形的產品外形,其路徑如圖1(b)所示,經過離散後的路徑轉換成每個點的座標系,再從座標點資料取得點跟點之間的X、Y、Z移動距離,這樣將輥頭移動至初始位置後,即會依照X、Y、Z三方向的移動距離作路徑上的移動。
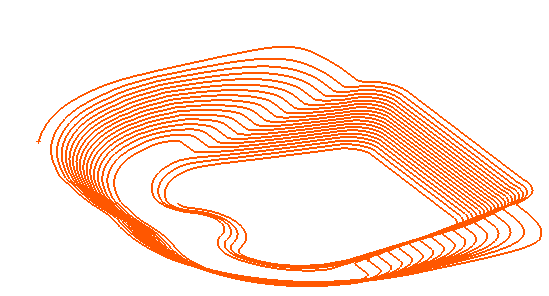
(a) (b)
圖1 (a)漸進成形產 (b)成形造型示意路徑示意
回文章內容列表更完整的內容歡迎訂購 2022年12月號 (單篇費用:參考材化所定價)