- 回首頁
- 機械工業雜誌
- 歷史雜誌
線控煞車系統設計之失效模式與效應分析
作者 簡明溫、呂銘宏
刊登日期:2024/04/01
摘要:本文以應用於自駕或先進駕駛輔助系統之線控氣壓煞車為主軸,依據新版 AIAG & VDA FMEA Handbook 之七步驟法,執行設計失效模式與效應分析 (DFMEA)。藉由結構分析,釐清整個分析範圍包含的系統、子系統和零組件及其連接介面與交互作用;繼而執行功能分析及失效分析,以識別其彼此間之功能關連性及失效關連性。根據風險分析結果,確認零組件之改善優先順序。最終,升級重要零組件規格,以優化失效預防措施;並藉由實驗室測試、台架驗證及實車驗證,以優化失效探測措施。經由 DFMEA 完整分析與優化措施,有效降低線控氣壓煞車系統設計之技術風險,並提升安全性與可靠度。
Abstract:This article focuses on the pneumatic brake-by-wire systems that are used in self-driving and advanced driver assistance systems. A comprehensive Design Failure Mode and Effect Analysis (DFMEA) based on
the seven-step method of the latest version of the AIAG & VDA FMEA Handbook was performed. Using the
structural analysis, this article clarifies the entire design analysis scope of the brake-by-wire system. Additionally,
this article performs the function analysis and the failure analysis to identify the functional correlation and failure
correlation among the system, subsystems and components. Based on the risk analysis results, the improvement
priorities of components are confirmed. Finally, this article upgrades the specifications of key components to
optimize failure prevention actions; and it optimizes failure detection actions through laboratory testing, bench
verification, and vehicle verification. The comprehensive analyses and optimization actions effectively reduce the
technical risks associated with the design of the brake-by-wire system, enhancing safety and reliability.
關鍵詞:線控煞車系統、失效分析、風險分析
Keywords:Brake-by-wire system, Failure analysis, Risk analysis
前言
車輛行業正面臨產品的技術複雜化、成本優化、不斷提高的產品安全性及可靠度品質要求,以及法規要求的產品責任等諸多挑戰。因此,車輛業為開發成功的產品,在開發過程中,需考量技術、財務、時程和策略等各種風險,並需應用各種方法與手段來降低風險。其中,失效模式與效應分析 (Failure Mode and Effect Analysis, FMEA)是一種以團隊導向、系統性、定性的風險分析與預防評估方法;該方法可有效地評估產品或製程失效的潛在技術風險、分析失效的原因和影響、提出失效預防措施及失效探測措施、追蹤並優化各種措施之有效性,以減少失效並提高產品和製程的安全性,從而降低產品開發的技術風險。
本文以應用於大型車輛自動駕駛系統或先進駕駛輔助系統的線控氣壓煞車為聚焦主軸,在線控煞車系統設計階段,根據最新版的 AIAG& VDA FMEA Handbook[1] 之七步驟法,執行設計失效模式與效應分析 (Design Failure Mode and Effects Analysis, DFMEA),以期提升線控煞車系統的安全性及可靠度。該七步驟法包含:準備與規劃、結構分析、功能分析、失效分析、風險分析、優化及分析結果文件化。藉由結構分析,產出圖像化的結構樹 (structure tree),以定義整個線控煞車系統設計分析範圍包含的系統、子系統和零組件及其連接介面 (interface) 與交互作用 (interaction)等關連性。其次,再藉由功能分析及失效分析,產出圖像化的功能樹 (function tree) 及失效網(failure network) 以識別系統、子系統和零組件之間的功能關連性及失效關連性。進而根據風險分析結果,訂定線控煞車系統零組件優化措施之優先順序 (action priority, AP)。最後,統整 DFMEA分析結果,採取優化的失效預防措施,將線控煞車系統重要零組件的規格,由原先的工業規格市售品升級為符合車規的市售品,並藉由實驗室測
試、台架驗證及實車驗證,優化失效探測措施。
DFMEA 分析標的之線控氣壓煞車系統
本文之線控氣壓煞車系統電控架構,如圖 1所示。其中,以虛線框表示之線控氣壓煞車系統包含:線控氣壓煞車模組、CAN/類比訊號轉換器、煞車電路切換繼電器及直流電源。圖 1 中之白底框零組件為原車配備,黑底框零組件為線控核心之整車線傳控制器,灰底框零組件則為線控煞車加裝之零組件。在維持原車氣壓管路最少更動條件下,線控氣壓煞車模組之輸入與輸出介面藉由並聯氣壓管路的方式連接至原車氣壓管路系統。當線控煞車功能啟動時,整車線傳控制器下達煞車控制命令以驅控電空比例閥開度,調節煞車壓力高低,進而控制煞車力道強弱;整車線傳控制器同時也致動煞車燈亮。本文使用之線控氣壓煞車模組零組件如圖 2 所示,重要零組件如電空比例閥、梭動閥及壓力感測器為工業規格市售品。
AIAG & VDA FMEA 之七步驟法
於 2019 年發行的最新版 AIAG & VDA FMEA Handbook[1] 之失效模式與效應分析的七步驟法,如圖 3 所示。失效模式與效應分析可分為針對產品設計執行的設計失效模式與效應分析 (DFMEA)及針對產品製程執行的製程失效模式與效應分析(PFMEA),本文聚焦於線控煞車系統之 DFMEA,依序扼要重點說明結構分析、功能分析、失效分析、風險分析及優化之目的、方法及結果。
結構分析 (Structure Analysis)
執行 DFMEA 結構分析之目的是將整個設計分析範圍可視化 (visualization),作為後續功能分析之基礎。DFMEA 結構分析藉由產出結構樹、方塊圖或邊界圖等圖像,以及識別連接介面、交互作用及零組件間之間隙 (clearance) 等,以釐清整個設計分析範圍包含的系統、子系統和零組件及其連接介面與交互作用等關連性。本文分析標的為圖 1 中之線控氣壓煞車系統,其四個子系統包含:線控氣壓煞車模組、CAN/ 類比訊號轉換器、繼電器模組及直流電源,而各子系統又包含各自之零組件。本 DFMEA 分析之「關注要素 (Focus Element)」設定為線控煞車之上述四個子系統,所以,在執行DFMEA分析時之「上一較高級別(Next Higher Level)」即為線控氣壓煞車系統;而「下一較低級別 (Next Lower Level)」即為各子系統各自之零組件。根據 DFMEA 結構分析所產出之線控氣壓煞車系統結構樹,如圖4所示。以「關注要素」之一的線控氣壓煞車模組為例,「上一較高級別」即為線控氣壓煞車系統;而其「下一較低級別」即包含圖 2 所示的 9 個零組件。
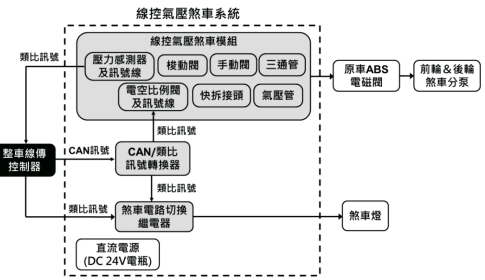
圖 1 線控氣壓煞車系統電控架構

圖 2 線控氣壓煞車模組零組件
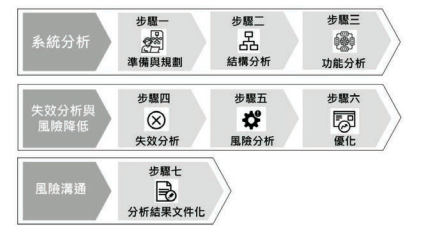
圖 3 AIAG & VDA FMEA 之七步驟法
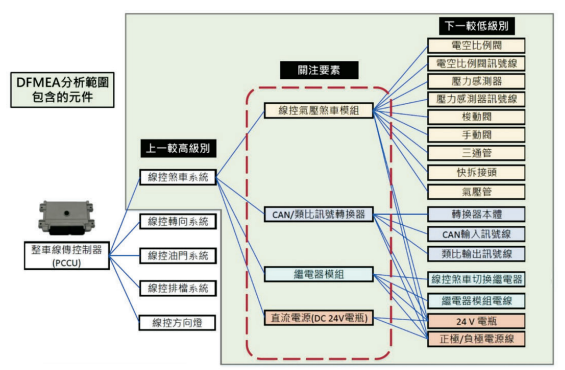
圖 4 線控氣壓煞車系統之 DFMEA 結構樹
回文章內容列表更完整的內容歡迎訂購 2024年04月號 (單篇費用:參考材化所定價)
主推方案
無限下載/年 5000元
NT$5,000元
訂閱送出