- 回首頁
- 機械工業雜誌
- 歷史雜誌
摘要
近年來,能源危機以及環境污染問題愈趨嚴重,電動車市場隨之蓬勃發展,快速高品質之鋰電池模組化技術需求因應而生,因此對於銅、鋁等金屬之同質或異質銲接需求日趨重要;掃描式雷射銲接具有加工速度快且不須保護氣體的優勢,本文將介紹掃描式雷射銲接技術以及該技術應用於鋰電池模組化之結果,並於文末介紹本技術已開發完成量產型設備並成功導入量產。
In recent year, energy crisis and environmental pollution problems are getting worse. The electric vehicle market has taken a huge leap forward, and the demand for rapid and high-quality lithium battery modular technologies has arisen. Therefore, the homogenous or heterogeneous metals welding technology such as copper and aluminum is becoming more and more important. The scanning laser welding has the advantages of fast processing speed and no need to protecting gas. This article will introduce the scanning laser welding technology and its application to the modularization of lithium battery. At the end of the article, the technology has been developed to complete mass production equipment and successfully introduced into mass production.
關鍵詞(Keywords)
雷射銲接、長距銲接、電池雷射銲接 Laser welding, Remote welding, Battery laser welding
前言
銲接是一種將兩種或以上材質,通過加熱或加壓的方式,使原子間結合而形成永久連接的技術。常見的銲接方法如氣銲、電阻銲、電弧銲、雷射銲接(laser welding)及電子束(e-beam)銲接等;其中,雷射銲接為非接觸式銲接技術,且因其具有熱輸入量低、銲道寬度小、殘留應力及銲接變形量小且不受電磁場影響等優點,而被廣泛應用於醫療、電子、汽車、船舶與航太等領域,其中又以汽車產業應用最為廣泛。
高能銲接設備主要是應用在需要高速、銲深厚度超過1mm以上的金屬銲接,其主要供應鏈體系分為高能雷射源、機械手臂、多軸加工平台、高能雷射銲接頭等廠商。根據美國市場調研機構Research and Markets發布的報告,全球雷射銲接機市場2017~2021年的年均複合增長率CAGR(Compound annual growth rate)將達到5.37%。現階段高能銲接的雷射源以光纖雷射及直接出光二極體雷射(Direct Diode Laser, DDL)為主,一般應用功率都在2 kW以上,目前常用的功率為4 kW及8 kW。光纖雷射源供應廠商有德國IPG、德國Trumpf、美國Coherent-Rofin、日本藤倉(Fujikura)、中國瑞科(Raycus)等,雷射功率大多在2 kW~8 kW。
近年來能源危機以及環境污染問題愈趨嚴重,電動車在全球引發熱潮,如特斯拉汽車(Tesla),且歐洲先進國家已大力推動2040年禁售燃油汽車,臺灣跟進訂定2035年禁售燃油機車,2040年禁售燃油汽車,汽機車電動化已是交通重點發展目標,國內外車輛電動化已成主流趨勢情況下,國內發展電動車相關生產技術刻不容緩,一台電動汽車包含三個主要核心零件:汽車動力電池、電機及電控,其中,動力電池在車輛成本中佔比最高,以日產Leaf為例,其所使用的鋰離子電池佔整車成本的60%,為其主要成本之所在,而動力電池模組也直接決定整車的性能。
動力電池主流為鋰電池,全球鋰離子電池供應廠商集中在亞洲地區,以韓、日、中廠商為首,最大電池組供應商為Panasonic/SANYO,其銷售量約占全球30%之多,其他的大型供應商有韓國SDI, LGC,日本SONY, Maxell, AESC(NEC), SGS及ATL,中國的比亞迪(BYD), BAK, Lishen等,而在中游的電芯產業部分,國際主要供應商有Sanyo, LG Chemical, Panasonic, SONY, SDI, BAK等,而在上游的正負極材料部分有Nichia, Umicore Korea, Toda Kogyo, BYD, AGC, Seimi Chemical等廠商。
臺灣在鋰電池產業鏈內有多家廠商分別投入研發與生產,在車用鋰離子電池產業鏈主要集中在上游正負極、隔離膜及電解液材料及中游電芯零件材料製造供應,此部分的產品在國際上尚具備競爭力,下游電池模組廠商面臨國外大廠的強力競爭,因此臺灣鋰電池產業發展策略不在於進行規模及價格競爭,而是凸顯產品開發的技術能力及應用端的整合能力。
電池模組之電極接合可分為兩大類,一種是扣件鎖合,技術簡單,但模組重量較重,後期有鬆脫的風險;另一種是電阻銲工法,製造速度慢,僅適用於較薄之金屬片。高速雷射掃描銲接技術因應而生,雷射掃描銲接具有速度快、熱輸入量小、可圖案變動等優勢,可滿足動力電池量產需求,並規劃將應用擴展至深具潛力市場產值的電動車相關零組件加工製造,帶動國內電動車產業發展。
掃描式雷射銲接技術
工研院雷射中心開發高功率掃描式雷射銲接製程技術,針對難銲金屬進行快速掃描式雷射銲接,傳統雷射銲接中以直寫式銲接為最常見的加工方式,圖1為直寫式與掃描式銲接頭。掃描式與直寫式兩者最大差異在於加工的速度以及是否外加保護氣體。掃描式雷射銲接藉由一組振鏡控制系統就可以進行一掃描區間內任意路徑的加工;而傳統直寫式銲接路徑則需掛載於平台或是機械手臂上進行加工,在加減速表現上不如掃描式來得迅速,故在銲接加工速度以及銲接路徑的自由度亦相對較低。而在保護氣體供給上,因為掃描式銲接速度較快(數百至數千毫米每秒),保護氣體供給較難搭配上如此的速度,若搭配環境控制腔體,則會大幅增加設備成本,而且在掃描式銲接的加工速度下,熱的累積相對於直寫式加工頭來小許多,此時持溫較短所生成的氧化銅不足以影響銲接品質,因此掃描式銲接系統通常會省略保護氣體。
以銅銲接為例,從圖2可得知在一般環境下的氧氣分壓進行銲接時會形成CuO氧化層(裂解溫度約1000 ℃),而掃描式銲接銅金屬時,溫度由1000 ℃冷卻至低於100 ℃的時間僅不到0.5秒,且在Yongfu Zhu [1]的研究中可觀察出於950 ℃環境下持溫7.2 ks僅產生約10 μm的CuO薄膜,故在以掃描式加工方式銲接銅時(持溫時間小於1 s),產生的CuO應低於2 nm。再加上應用領域屬高電流應用(high current)而非高頻應用(high frequency),電流流通以金屬內部為主,故表面所生成的氧化層對於鋰電池領域的應用視為可忽略。由此判斷,雖然在掃描式銲接下無保護氣體防止金屬表面氧化,但其作用時間不足以生成影響品質的氧化層,使得此方式的銲接在氧化品質上並無太大疑慮。

(a) (b)
圖1 銲接加工頭,(a)直寫式銲接頭;(b)掃描式銲接頭
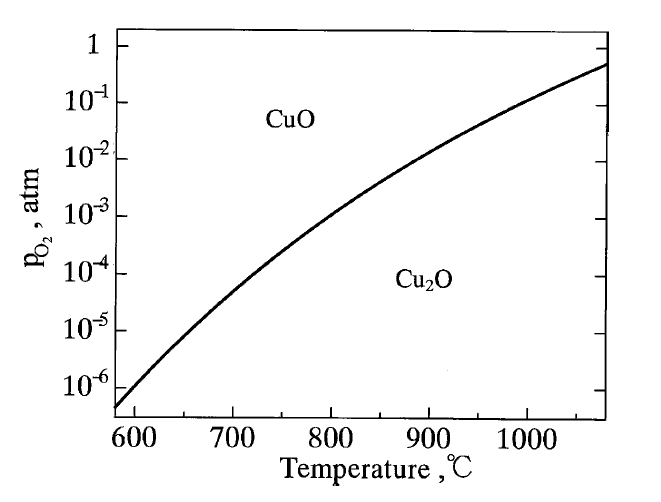
圖2 CuO與Cu2O平衡圖 [1]
更完整的內容歡迎訂購
2020年02月號
(單篇費用:參考材化所定價)
主推方案
無限下載/年 5000元
NT$5,000元
訂閱送出